Better building with rotating telehandlers

Partner Content produced by KHL Content Studio
16 April 2024
Telescopic handlers are unquestionably one of the most useful pieces of equipment on the job site. The “Swiss Army Knife” of construction, due to the number of tasks they’re capable of, these machines are often the first on the scene and the last to leave.
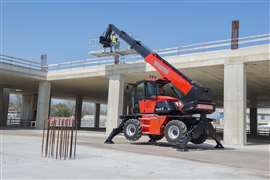
Rotating telehandlers, for their part, provide a literal twist on the concept, offering a wide range of advantages compared to their traditional, drive-and-place counterparts.
Manitou has a long history with telehandlers, having launched its first drive-and-place model in 1981, followed by the rotating MRT 1540 in 1993. The West Bend, WI-based manufacturer now offers 11 rotators in its MRT Series, the largest with a maximum lift height of 113 feet and a max capacity of 15,400 pounds.
Its well-established line of drive-and-place machines includes 29 models ranging from the ULM 412 (2,200 lbs. capacity) to the MHT 12330 (73,000 lbs. capacity).
“Throughout those decades of history with telehandlers, Manitou has seen rotators gain significant popularity in recent years – particularly in Europe. While still considered by many here in North America to be a relatively new idea, their time has come,” says Steve Kiskunas, product manager for telehandlers at Manitou, pointing to three primary advantages they can offer.
1. Increased productivity
Through enhanced efficiency and versatility, rotating telehandlers offer improved productivity - arguably the most important goal on the job site.
For starters, rotating telehandlers have higher lifting capacities than drive-and-place machines, allowing for heavier loads to be lifted and transported, reducing the number of lifts required.
“If you’re looking to go above 56 feet, standard telescopic handlers generally don’t go there,” explains Kiskunas, noting that the ability to turn 360 degrees continuously means operators can reach previously inaccessible areas.
Rotating machines don’t need to be constantly repositioned, so operators can save a significant amount of time and effort during tasks.
“It’s much quicker to have the machine stationary and use the rotating feature to pick and place materials,” notes Kiskunas. “It really speeds up the material placement process. You’re moving more material per hour with a rotating machine than you would with a traditional telehandler.”
The ability to rotate also allows operators to access confined spaces more easily.
“If you’re on a city street or sidewalk and only have a very small space to unload trucks and deliver materials to the job site, the rotating machine offers a big advantage,” says Kiskunas.
“These machines are ideal any time you have restricted access to a job site or a limited amount of space, such as highly populated urban areas, or in applications where you don’t have a great deal of space for storing the materials,” he says.
This versatility offers tremendous flexibility in job site operations, minimizing the need for multiple machines and optimizing resource allocation.
“Properly equipped with the right attachments and a properly trained operator, a rotating telehandler can take the place of three different pieces of equipment – telehandler, mobile elevating work platform and light crane (under 7metric tons),” notes Rob Stanton, business development Manager, MRT/MHT Central U.S.A. Manitou Group.
“You’ve got multiple contractors on site, multiple things going on, and this is one less piece of equipment moving around that job site that could breakdown,” Stanton continues. “Our most successful customers will have regular telehandlers or forklifts feeding that rotating telehandler to take materials up to wherever they’re needed. That’s the most beneficial use of time and machines.”
2. Improved operation
Rotating telehandlers offer enhanced operational features compared to traditional drive-and-place machines. To start with, the 360-degree rotation capability allows operators to have an unobstructed view of their surroundings.
This improved visibility ensures operators can maneuver the telehandler with precision. Meanwhile, the load management feature on the Manitout MRT Series assists operators in achieving effective handling.
“Our rotating telehandlers have a load management system that will stop any movement of the machine until you get back within the correct operating load limits. The load management system is one of the most important advantages of rotating machines,” notes Stanton.
3. Cost savings
Equipment acquisition and ownership costs are a crucial consideration, and rotating telehandlers do have a price tag that’s one third higher than their drive-and-place counterparts. That increase in upfront cost can be made up over time through increased efficiency, however.
“Our current 10,000-pound, 55-foot standard telescopic handler has a list price that’s approximately two thirds that of a rotating machine with the same capacity,” says Kiskunas. “But the major components are very similar to a traditional machine, and there’s not a significant difference in the standard maintenance schedule.”
At the end of the day, the increased versatility of rotating telehandlers allows operators to handle a broader range of tasks with a single machine, eliminating the need for multiple specialized machines on site.
For example, with Manitou’s work platform attachment, it’s not necessary to bring in a dedicated mobile elevating work platform.
Stanton recalls showing a group of contractors how the work platform attachment works and their reaction to its efficiency.
“I spent the whole day teaching a group of contractors about the entire machine, with attention to work platform set up and operation. We also went over how to use the machine in full wireless remote mode for other attachments,” he says. “The machine we were on goes up about 82 feet, and we went up with four guys in the basket. It will hold 2,200 pounds.”
Stanton adds, “The guys were very excited, they said, ‘This is going to save us so much time, two guys can do the job of six now’.”
Similarly, with a lifting hook or jib attachment for suspended loads, there’s no need for a boom truck crane.
“Contractors get excited about the ability to lift higher without needing to bring in a standard crane rental or another piece of equipment to do the work,” Kiskunas says, noting rotating telehandlers are not construction cranes and don’t meet the North American Crane standard.
“They can perform many of the tasks that a standard crane would do, just with limited capacity,” Kiskunas says. “A standard crane can lift 35 tons, while these machines are going to max out at eight tons.”
The rotating telehandler’s ability to tackle many tasks can reduce capital expenditure and maintenance costs associated with maintaining a fleet of different machines. Additionally, their improved efficiency and productivity can result in faster completion of tasks, reducing labor costs and increasing overall profitability.
Why don’t we see more of these on today’s job sites?
Despite the benefits, rotating telehandlers are still seeing relatively slow adoption in North America. Why?
“One of the reasons is we’re still learning how to use this equipment and make it work on our job sites,” Kiskunas explains. “It really is changing the way we think about bringing materials to the job site and placing them where they’re needed.
“Having a stationary machine and then rotating to place the materials changes how you set up your job site and how you approach building the structure.”
Kiskunas says as more and more contractors start to see the benefit in efficiency and productivity from rotating telehandlers, adoption will continue to increase.
Will a rotating telehandler work for you?
There are three things you should think about when looking at your lifting needs, Kiskunas says.
“The first one is maximum working height, then second is working capacity. These are dictated by what material you are trying to lift, how far you need to place it, and where you’re going to take that material.
“The third thing would be the setup area. How much room do you need to set a piece of equipment in place? This information will vary from model to model, based on the lifting height and capacity of the machine.
“A 10,000-pound machine needs a 16-foot by 15.5-foot area to set up front and rear outriggers. You need to fully extend the outriggers to gain maximum capacity,” Kiskunas explains. “You can operate the machine with the stabilizers at a smaller footprint, if it’s necessary, but then your capacity is reduced.
“It really is a different way of thinking about how you’re going to build your building when you go with the rotators,” Kiskunas says. “This isn’t just a question of selecting the right piece of equipment, it’s thinking about how the entire project is going to come together, from how materials are going to be delivered and where they will be staged and so on.”
Stanton says rotating telehandlers can simply speed up construction: “I’m thinking about a project where custom homes are being built. Traditionally, you’d put down the foundation, and then you’ll have the rough lumber brought in for framing, and suddenly, you’re ready for the next story. Traditionally, you’d have to wait until you get a crane out there to do the rest of the work.”
Stanton continues, “Builders have lifted walls up with the MRT and are ready to go to the next story. They don’t have to contract a crane to come out to set floor joists for the second floor. They can do it all there, or if they’re putting trusses on right away, they’re ready to go.
“The speed of having the materials there definitely changes the process; you need to have everything there because you could be done setting walls in a day, when it used to take three days. Now you’ve got a machine that can do it all, and it can speed things up quite a bit,” he says.
Kiskunas adds, “If we could, we’d have a bumper sticker that says ‘Try it, you’ll like it,’ because generally we find that contractors who start using rotators find not just a very useful tool, they also find other ways of doing traditional tasks that they hadn’t even thought about. These machines open up a great deal of flexibility and versatility for the customer.”
Partner Content
This article was written for Manitou by KHL Content Studio.
CONNECT WITH THE TEAM

