World Demolition Awards Shortlist - Safety & Training
29 August 2024
D&Ri is pleased to announce the Safety & Training category shortlist for the 2024 World Demolition Awards, which will take place on 6 and 7 November October in Stockholm, Sweden, as part of the World Demolition Summit.
Congratulations to the following companies who made the Safety & Training category shortlist.
World Demolition Awards 2024 - Safety & Training Shortlist
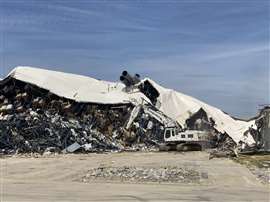
BRANDENBURG
COUNTRY: United States
PROJECT: Ramboll Group/Pfizer Rocky Mount
While performing a complex selective removal project at a Pfizer manufacturing facility, Brandenburg relied on its thorough and complete site safety training to take shelter in the dedicated safety area as a tornado ravaged the facility.
Two essential warehouses were destroyed or left in an unsafe condition after an EF3 tornado ripped through Pfizer’s 250-acre pharmaceutical manufacturing complex in Rocky Mount, North Carolina in 2023.
Brandenburg employees quickly shifted focus to clear the rubble and remove all or parts of the warehouse buildings. Safety was top priority to protect the team as well as other contractors and Pfizer employees.
Efforts began with an Engineering Survey, followed by utility capping, development of a site-specific Health & Safety Plan, a comprehensive Methods Statement, Job Safety Analyses, and Safety Task Analysis Cards for all on-site team members.
Special safety measures were designed to protect employees from potential opioid exposure, a danger created because more than 40,000 pallets of damaged and destroyed boxes of pharmaceutical products were strewn throughout the wreckage.
The company worked in unison with its Occupational Health Provider to analyse potential scenarios. It also made sure to have a supply of Narcan on-site and trained each of its employees in its use and application. Narcan is the recommended treatment for Opioid exposure which was one of the products affected by the tornado.
The complicated and arduous task of clearing the natural disaster damage was completed on time, on budget, with no reported health and safety incidents.
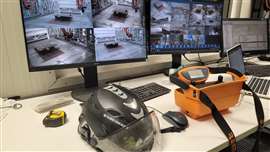
DESPE
COUNTRY: Italy
PROJECT: Kryalos Disaster Recovery
Despe was contracted to the “disaster recovery” operation that was implemented after a storm of water and wind that hit the geographical area of Milan, Basso Varesotto and Brianza in July of 2023.
In the former Alfa Romeo industrial area of Arese, logistics centres were built in warehouses built in the 1960s/70s and divided by brick and plasterboard walls.
As a result of the fierce winds and torrential rain that swept through the industrial complex, a long section of the wall collapsed to the ground, simply due to the vertical presence of high shelves containing goods to be shipped.
The danger of the demolition operation was due to the instability of the entire system, which was severely compromised.
From this problem the winning solution was found, namely the use of radio-controlled excavators. In addition to the difficulty related to the instability of the wall to be demolished, was the presence of electrical and fire-fighting systems to be preserved and interfering with the activities.
The use of radio-controlled equipment ensured maximum operator safety, as the operator was not in the area, but in the control room in front of a computer.
The project required Despe to stop the activities of the logistics companies involved, who were tenants of the warehouses involved, restore the usability of key areas, carry out the inevitable demolition of the collapsed walls safely, accelerate the timeframe as much as possible in order to limit disputes and site disruptions with the tenants.
DESPE
COUNTRY: Italy
PROJECT: Garigliano Cutting Station
Despe designed and constructed a cutting station for large contaminated components equipped with autonomous ventilation and ionising radiation control systems, for the decommissioning of contanminated nuclear plant components.
From the control room the operators could utilise pre-set cutting sequences or act directly via radio control, while the torch can make precise cuts up to 100 mm thick and is equipped with an anti-collision system to prevent accidents.
The cutting function was carried out by a teleoperated machine, i.e. a gantry equipped with two anthropomorphic robots for the execution of oxyfuel cutting and handling of contaminated components from the decommissioning of a nuclear plant.
Despe’s operator was able to monitor the cutting process from every angle via cameras, with the works were carried out in compliance with the ALARA Principle, to minimise the risk of contamination and radiation that would otherwise have been present due to the heat of oxyhypropane cutting.
The use of the teleoperated machine also limited personnel access, with workers only allowed access for secondary operations such as cleaning the area, positioning the components to be cut and clearing the segments not handled by the robot.
The entire design, realisation and testing of the two robotic arms was performed by DESPE.
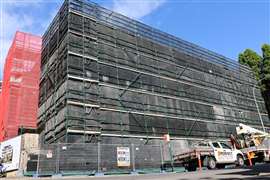
PERFECT CONTRACTING
COUNTRY: Australia
PROJECT: Elizabeth Bay
Located in Sydney’s eastern suburbs, the Elizabeth Bay project undertaken by Perfect Contracting involved a six-storey residential building faced by regulatory constraints that prohibited new construction of the same size.
The existing structure required significant reinforcement to meet modern building codes, necessitating the implementation of innovative bracing and structural support solutions.
With meticulous planning and execution, Perfect Contracting achieved an impressive 39,000 labour hours without a single injury, demonstrating its unwavering commitment to safety.
Regular safety talks, rigorous risk assessments, and the use of appropriate personal protective equipment (PPE) were integral components of the safety protocols that ensured a secure working environment for all team members.
The company utilised custom-fabricated brackets and plates that were created specifically for the unique structural needs of the building. Complex logistics were adeptly managed, with the team overcoming narrow roads, heavy loads and site constraints without the use of cranes. Careful monitoring was conducted to avoid deviations in 3D data models, ensuring precise execution of the project plan.
Sustainability was another key focus, with up to 95% of mixed waste and 100% of rubble, concrete, bricks, and metal being recycled. Perfect Contracting’s approach combined innovative engineering, strict safety protocols, and sustainable practices, highlighting its ability to deliver complex projects with precision, safety, and environmental consciousness.
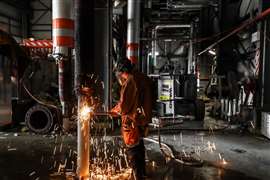
WARD DEMOLITION
COUNTRY: New Zealand
PROJECT: Southdown Power Station
Ward Demolition’s work at the Southdown Power Station involved the demolition of the sites cooling towers, which were situated within 3 metres of live suspended 11-KV cables.
The company’s team operated in close proximity to a live high voltage major switch yard and overhead powerlines running alongside the length of the site throughout the duration of the project. These hazards caused great concern for the project client(s), especially around vibrations, which resulted in increased heights work and crane lifts, and therefore increased immediate risk to Ward’s team.
In addition, Ward’s team also had to navigate conflicting health and safety policies and procedures in order to carry out the works safely.
One area in particular that presented a challenge was the power station’s own health and safety governance, which included a no dropping policy and a requirement to have a spotter accompanying every machine.
This meant that Ward was not allowed to pull over the site’s two boiler stacks and chimney, as the key concern was around vibration, and also presented greater risk as additional crew members would have to be in close proximity to machines in operation.
In a power station maintenance setting this policy is valid because there’s little need for this action and dropping something would be dangerous and unexpected. However, in demolition controlled drops in designated areas with barriers and spotters are allowed because it is often the safer option.
Through communication, consultation and cooperation with its client(s) and project partners, Ward executed the safe cutting of the top exhaust sections and craned them out before using two high reach excavators to lower each bundle one by one.
CONNECT WITH THE TEAM

