World Demolition Awards Shortlist - Industrial
29 August 2024
D&Ri is pleased to announce the Industrial category shortlist for the 2024 World Demolition Awards, which will take place on 6 and 7 November October in Stockholm, Sweden, as part of the World Demolition Summit.
Congratulations to the following companies who made the Industrial category shortlist.
World Demolition Awards 2024 - Industrial Shortlist
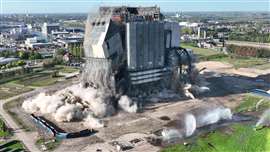
BROWN AND MASON
COUNTRY: United Kingdom
PROJECT: Gelderland Power Station - Nijmegen
CLIENT: Engie
Brown and Mason Group (BMG) were contracted by the multinational energy company Engie to undertake the decontamination, dismantling and demolition of their Gelderland power plant.
The contract involved substantial asbestos removal and extensive use of explosives all within the timeframe of Brexit, Covid and the war in Ukraine.
Centrale Gelderland, a 585MW coal/biomass-fired power plant located in the city of Nijmegen was the first in The Netherlands with a flue gas desulphurisation installation that provided a reduction in sulphur emissions of up to 90%, with the LowNOx burner reducing the formation of nitrogen oxides by 50%.
The 1994 constructed DeNox further reduced nitrogen oxides with use of a catalyst. Large dust collectors and electrostatic filters removed around 99.9% of fly ash particles from the flue gases before they left the plant through the chimney.
Engie’s facility had been at the mouth of the Maas-Waal Canal since 1936. The power plant was constructed on the bank of the river Waal bordering the Maas-Waal Kanaal to the North, to the East and to the South of the site the power plant was boarded by heavily mixed industrial and residential estates.
The site contains photovoltaic parks and an electrical substation which form part of the national infrastructure powering the City of Nijmegen, and located to the site’s western boundary is the district of Weurt, a very sensitive and affluent residential area, a political ‘hot potato’ with the historical operations of Centrale Gelderland Power Plant and other industrial operations. Contract Complexity.
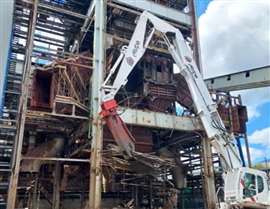
DESPE
COUNTRY: Italy
PROJECT: UNIT 1, MERCURE POWER PLANT
CLIENT: Mercure Srl
The project to demolish Unit 1 of the Mercure power station was particularly challenging.
The customer required that the demolition of the boiler and back boiler plant be carried out without disrupting the production of Unit 2, which is located directly next to it.
Another particularly complex aspect was the safeguarding of the lift shared by the two units. The lift structure had to be reinforced during the dismantling phase of the side-by-side boiler to replace the static constraints that were gradually being removed.
In addition, the demolition window had to be limited to 7 months to avoid disruption to the fuel supply phase (wood chips). The disruption also had to be managed by minimising the storage of demolition materials on site.
Despe took up the challenge and immediately proposed its own system for lowering the pressure parts of the boiler. This system is characterised by hydraulic jacks placed on the roof of the boiler, capable of taking the full weight of the combustion chamber and the pressure parts system and lowering them progressively towards the ground.
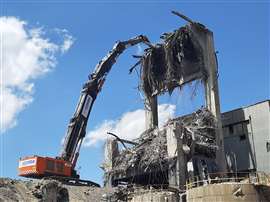
LEZAMA DEMOLICIONES
COUNTRY: Spain
PROJECT: La Robla Thermal Power Plant
CLIENT: Naturgy
This project comprised the demolition of two slender chimneys measuring 200 m and 120 m in height, as well as the felling of two, 100-m high cooling towers, which were demolished via a simultaneous explosion - which was reportedly the first to involve two cooling towers ever carried out in Spain.
Lezama also carried out the removal of La Robla’s two boilers, measuring 82.3 m and 54.1 m high and with an apparent volume of 185,175 cu m and 93,744 cu m respectively. The structures were composed of materials as diverse as fiber cement, insulation and various metals such as iron, stainless steel and copper
This disparity in composition is a great challenge, since it is essential to separate these materials at source in order to use the waste for recycling. In addition, work was carried out to dismantle the turbines of the generating sets and their concrete bench, the building that housed it and the auxiliary structures that connected all these elements of the thermal power plant.
All the work was carried out using the principle of selective demolition, with the materials separated at source to minimise the production of waste sent to landfill.
Potentially contaminating materials such as fuel oil, diesel, ash and other products were removed from the facility, with dangerous waste - such as asbestos and fiber cement - also removed.
At its peak, more than 100 people were contracted by Lezama to work on the project, with almost 30 more brought in as subcontractors.
The company, which provided monthly environmental footprint reports to the client and other project partners, achieved a C&D materials recovery of nearly 95%. Additionally, more than 80 pieces of equipment, as well as stores of chemicals, from the facility were sent to other industry operators for reuse.
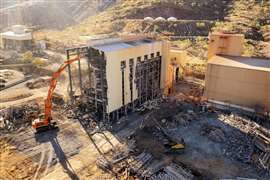
LIBERTY INDUSTRIAL
COUNTRY: Australia
PROJECT: Argyle Diamond Mine Closure Project
CLIENT: Rio Tinto
The Argyle Diamond Mine, located in the East Kimberley region of Western Australia, was a significant diamond producer, notably providing over 90% of the world’s pink and red diamonds.
Following its closure in November 2020, Liberty Industrial was contracted by Rio Tinto to deconstruct, demolish, and remove all infrastructure within the mining lease, covering an area approximately 50 hectares in size.
The scope of work included the dismantling of the process plant, mine camps, power station, and airport, as well as the remediation of contaminated areas.
Liberty Industrial employed advanced methodologies, including the use of high-reach demolition excavators, 3D modelling for induced collapse, and strategic waste management.
The project focused heavily on recycling, achieving the shipment of 34,000 tonnes of ferrous material, 1,000 tonnes of non-ferrous material, and 875 tonnes of HDPE piping, contributing to environmental sustainability and resource conservation.
Challenges such as COVID-19 restrictions and the site’s remote location required innovative solutions, including the relocation of personnel and the establishment of a self-sufficient site. Additionally, collaboration with Traditional Owners ensured fair work opportunities and engagement, resulting in significant local participation.
The project concluded successfully on April 15, 2024, within the closure timeframe and budget. Liberty Industrial’s efforts were recognized with the Global Rio Tinto Safety Award for Best Contract Partner for the Argyle Diamond Mine Closure Project in June 2023.
The project set a precedent for Traditional Owner engagement and demonstrated the efficacy of Liberty Industrial’s strategic planning, efficient use of state-of-the-art equipment, and strong stakeholder collaboration.
MGL DEMOLITION
COUNTRY: United Kingdom
PROJECT: Redcar Coke Ovens By-Products Plant, Phase 2
CLIENT: South Tees Development Corp
MGL Demolition (MGL) was a key contractor in decontaminating and demolishing the former Redcar Coke Ovens By-Products (RCOBP) Plant. This complex and challenging demolition project supported the redevelopment of the former Redcar Steelworks site, Teesworks, the UK’s largest industrial zone.
The RCOBP Plant contained many toxic, flammable, and pyrophoric materials throughout the site. Several years earlier, it had been shut down but not decommissioned, and it was in poor condition with limited records of remaining materials.
MGL developed various techniques to safely decontaminate, demolish, and clear the site for redevelopment. By dividing the site into six zones based on risk profiles, MGL conducted additional sampling and analysis to determine the best decontamination and demolition methods.
The company used dry recovery, steaming, chemical treatment, foam blanketing, and conventional and explosive demolition to safely remove the contaminants and demolish the structures, a testament to its adaptability and problem-solving skills.
These techniques minimised the quantities of hazardous wastes and facilitated the safe and efficient recovery of all metals for recycling.
Prioritising local employment, MGL supported the skills academy and contributed additional personnel resources to ensure local people were well-equipped to take advantage of the new job opportunities created by the project. This was a key factor as the client progressed in the regeneration and redevelopment of the site.
This project has been one of Teesside’s most complex and challenging demolition projects. Over 25,000 operative hours were safely undertaken with no major incidents.
CONNECT WITH THE TEAM

