Project Report: Redcar Coke Ovens By-Products Plant Phase 2 Demolition
03 March 2025
Buried beneath years of industrial decay, hazardous chemicals and unstable structures made the Redcar Coke Ovens By-Products Plant a demolition project like no other. This is how MGL Demolition took it apart—safely, strategically, and with the environment in mind.
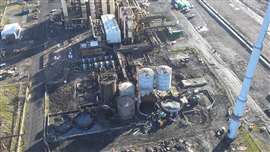
When MGL Demolition Ltd (MGL) took on the task of dismantling the former Redcar Coke Ovens By-Products (RCOBP) Plant, they were stepping onto a site frozen in time—a relic of the industrial past, littered with hazardous materials and decaying infrastructure.
The plant, once an integral part of the steelmaking process, had been left to deteriorate for years, its tanks, pipes, and machinery still holding the ghosts of its former chemical processes.
The challenge wasn’t just to bring it down, but to do so safely, methodically, and with a firm grip on environmental responsibility.
Work officially began in May 2022, with the first priority being a comprehensive risk assessment.
The site was far from straightforward—layers of contamination had built up over decades, and remnants of hazardous chemicals lurked in storage tanks, underground pipelines, and process vessels.
Hazardous Materials & Risk Mitigation
Before any demolition could begin, the MGL team needed to tackle decontamination.
This meant deploying a combination of steam treatment, chemical dosing, and a remote-operated cleaning cannon system (ROCCS) to safely remove contaminants without requiring personnel entry into confined spaces.
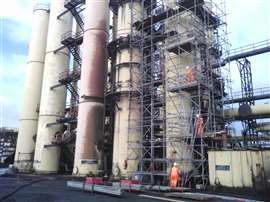
Each phase of demolition was dictated by the hazardous materials involved. Compiling a hazardous waste inventory that would provide the risk profiles for the work to be carried out and correct waste disposal routes.
As well as toxic materials, the presence of pyrophoric substances that could ignite when exposed to air, were a significant concern in the pipework and treatment plants.
To mitigate these risks, nitrogen blanketing was used to displace oxygen and prevent unwanted reactions.
When sections of plant and pipework needed to be taken offline, a coordinated effort between demolition teams and environmental specialists ensured a controlled process.
Blasting Tall Structures
Explosives played a role in the removal of some of the site’s largest structures.
The Gas Holder and Ammonia Flare Stack, towering reminders of the plant’s former operations, were earmarked for controlled explosive demolition. But before they could be brought down, extensive pre-weakening was carried out to direct the collapse safely.
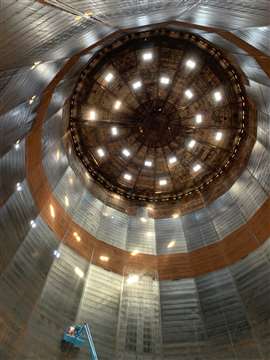
Structural engineers and regulatory bodies signed off on the plans, and test detonations were conducted to verify the effectiveness of the approach, which saw the use of both cutting and kicking charges.
When the moment came, the demolitions proceeded exactly as planned, clearing the way for the next stage of the project.
The environmental impact of the demolition was carefully managed. In total, over 98% of waste was diverted from landfill, with more than 5,000 tonnes of scrap metal recovered for recycling.
Almost 6,400 tonnes of hazardous waste was assessed, with over half of it converted into energy and nearly 42% treated and recycled.
Only a small fraction—just over 2%—required disposal in landfill, a testament to the efficiency of the waste management strategy. In addition, site-generated crushed materials were repurposed for backfill, reducing the need for imported fill material.
Ensuring Demolition Site Safety
Ensuring the safety of the workforce, which at its peak saw 30 individuals working on the site, was paramount.
Gas monitoring systems were in place throughout the project, constantly checking for the presence of toxic gases such as ammonia, benzene, and hydrogen sulfide. In total,over 25,000 hours were logged on-site without a significant incident
With two twelve-hour shifts running daily, safety protocols were rigorously enforced, including structured safety briefings, ongoing site inspections, and emergency response planning.
Every aspect of the work was designed to prevent accidents and keep workers protected in an unpredictable environment.
Construction Technologies
Modern demolition technology played a key role in making the project efficient and controlled. Digital technologies utilised during the works included BRE Smartwaste and Donseed Biometric Site Management sign-in/out system, as well as other specialist technologies for detecting hazardous materials, toxins and gases.
High-reach and demolition excavators, which included a Liebherr R954C and three Komatsu machines fitted with specialised shears and pulverizers, methodically dismantled structures, minimising airborne dust and vibration.
In high-risk areas, remote-controlled demolition units took over, ensuring that human workers were kept out of harm’s way.
Dust suppression measures, including misting systems and water cannons, were deployed to prevent the spread of particulates beyond the site’s boundaries.
Skills support and development
Beyond the technical aspects, the project had a strong community engagement element. A Skills Academy was set up to provide training opportunities for local workers, ensuring that the knowledge and expertise gained from this complex demolition could benefit future projects.
Nearly £20,000 (US$25,000) was also donated to local initiatives, and 254 volunteer hours were spent on community programs. On-site mental health support initiatives were introduced to provide employees with resources and counseling, recognizing the importance of well-being in high-risk work environments.
With the last of the hazardous structures removed and the site cleared, the land was ready for redevelopment as part of Teesworks’ broader industrial regeneration plan.
The successful execution of the project ensured that future developments could proceed without the legacy issues of contamination and structural instability.
Project Completion & Site Legacy
Utilising a phased completion plan, MGL Demolition handed over detailed documentation to the client, outlining the decontamination measures implemented, waste management outcomes achieved, and the final condition of the site.
This project wasn’t just about demolition—it was about transformation. What had once been a hazardous, deteriorating industrial site is now a space with new potential. The combination of careful planning, adaptive demolition techniques, and environmental responsibility ensured that this site, once a key part of Teesside’s industrial history, could now play a role in its future.
CONNECT WITH THE TEAM

