Onboard displays for off-highway machines
12 August 2024
Danfoss Power Solutions is active in many areas of machine technology development, from powertrain components, through to hydraulics and data collection. In this article, Power Progress International interviewed two experts from DPS to find out more about the latest telematics and HMI strategies for off-highway applications.
Power Progress International: In basic terminology, can you explain how the data/information displayed on the cab screens is accessed – is it directly from the machine/ECU, or via an OBD II connection (as in most passenger cars)?
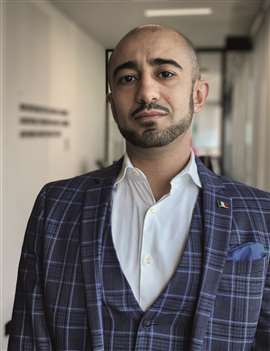
(MAES) Mohamed Abd El Salam, senior portfolio manager, IoT & Connectivity, Danfoss Power Solutions: Data displayed on cab screens is captured via CAN signals received from the engine and system connected to it, which is mainly the ECU and sensors.
From an IoT point of view, data is accessed through the CAN bus or CANopen network that is similar to the automotive world, but slightly different as it is not always standardized like OBD II. So, in several cases, data will need to be parsed properly to get a meaningful value.
Data can also be retrieved directly from specific sensors if those sensors are not digitalized and thus not broadcasting data on the CAN bus. In that case, the electrical specs of the sensor must be known to identify, for example, the relation voltage/dimension value.
PPI: Are larger screens in off-highway machines a function of lower screen prices or the need to display more detailed information on a single screen?
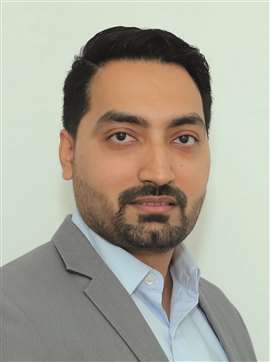
(HO) Herman Oberoi, senior portfolio manager, Displays, Danfoss Power Solutions: It’s a combination of lower pricing and the need for more information that’s driving the trend toward larger screen sizes. Space management requirements in new cabin designs are another influence; this creates a need to show consolidated, yet more detailed, information on bigger screens in one glance.
PPI: While a higher screen resolution can potentially allow more information (dials, graphs, etc.) on a given screen, is there a need to make the graphics larger to allow faster analysis of machine operating levels?
HO: Yes. Alongside larger screens, there’s a need for larger graphics which offer a clear view of relevant details. Gauges are a good example where readability is important.
PPI: Is there any drawback to using info screens in battery-electric machines?
HO: It depends on the application size requirements and how many individual gauges are in use in the application. But there are no direct drawback because a screen draws less power in comparison to analogue gauges and clusters. In addition, it gives the user the advantage of much more information on one display.
PPI: Will a greater depth of telematics information be available in near-future HMI systems, allowing the operator to have a better understanding of machine condition?
MAES: Greater use of telematics data in HMIs is something we see happening already, with other areas coming soon. It all depends on what the machine manufacturer wants to program into the display. A few use cases include notification of available software updates, real-time views of machine conditions pertaining to predictive maintenance, and other OEM-specific performance compliance parameters to provide add-on services. An important consideration for software updates is operator involvement. An operator must approve the installation of new machine software for safety reasons.
We’re seeing a lot of bidirectional communications between machines and portals enabled by telematics. To lessen the processing load, data that’s collected on the machine is ideally sent offboard for processing. OEM recommendations generated from that data – the machine requiring inspection or service, for example – is then sent back to the machine HMI for the operator to act upon. This can be a technique for OEMs or dealers to sell services and maintenance programs. Another example could be work tracking, where a machine operator can indicate through the display that a project or task for a specific customer has been completed, which would then send a message back to a portal at the business office.
PPI: How will AI help to remove related complication from the HMI systems? Can AI be relied upon to make critical machine operation decisions?
MAES: AI, especially generative AI, is creating a lot of opportunities and breakthroughs in many industries. The off-highway industry is still exploring how to best utilize the tech to increase productivity and efficiency of machines and operators. As algorithms evolve with more self-learning codes, AI can provide many opportunities to simulate machine environments virtually and facilitate testing of new applications faster and more conveniently.
Autonomous functionality could certainly embrace AI, especially where a machine can take over for the operator to perform a task more precisely or safely. As for whether AI can be relied upon to make critical operation decisions, this is a possibility, but it might be pushed to the operator as a recommendation via HMI – maybe never executed in a fully autonomous way. The regulations and legislation around AI are still not clear, but we will probably see greater clarity and alignment in the next few years.
“The regulations and legislation around AI are still not clear, but we will probably see greater clarity and alignment in the next few years.”
-Mohamed Abd El Salam, Danfoss Power Solutions
PPI: There is a minor backlash in the passenger vehicle market, where OEMs are dialling back on incorporating all vehicle functions on screens and adding more physical/direct buttons (particularly for fundamental operations, HVAC, etc.). Is the same being seen in the off-highway market?
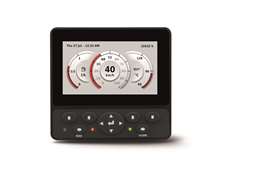
HO: The off-highway market tends to follow the passenger car market in terms of HMI trends. We are also seeing some inclinations to stick with physical buttons, as well as CAN keypads on the armrest, in some regions and for certain applications where safety concerns are higher.
In China, many of the off-highway OEMs we work with prefer displays with buttons. They typically have at least eight to 10 buttons that are configurable for operation shortcuts and views of particular screens. The same is also true for a lot of OEMs in Europe.
Similarly, in certain applications – machines used in mining or on difficult terrain, for example – the operator is not supposed to look at the screen frequently. Having CAN keypads on the armrest or buttons for quick info shortcuts can help the operator focus on the task without spending time navigating through screens to find specific information.
PPI: Is there an industry-accepted hierarchy of information as displayed on screens, to allow faster access to critical information and to support operators as they move between machines?
HO: We’re not aware of a standard hierarchy for information displayed on screens.
PPI: Touchscreens are notoriously temperamental, in that temperature and dust can affect basic touch function. Many cannot be operated while wearing gloves (unless there is a special touch surface on the glove). What can be done to improve this – can the touch matrix be improved to ensure that a virtual button press will illicit the required response?
HO: The ability to operate a touchscreen display while wearing gloves is a requirement in off-highway machinery. This requirement can be fulfilled through the use of resistive touchscreen panels instead of capacitive touchscreen panels. Additionally, the user menu should be designed to avoid accidental touches, and critical items are usually subject to confirmation prompts.
PPI: Do scratches on the touchscreens also inhibit correct functionality? If yes, what can be done to eliminate this issue?
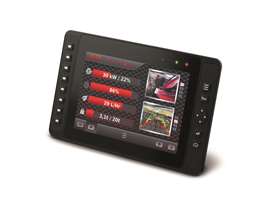
HO: Yes, scratches can inhibit the touch capabilities, as well as the viewability of the screen. There are more rugged screen types available that provide better protection against scratches. While more expensive, it makes sense to consider these for the more severe applications in the off-highway industry. The Danfoss DM series is an example of displays that make use of this more rugged screen type. Danfoss tests and selects screen components designed to withstand rough handling. The DM series displays have been tested and proven to withstand a 536-gram ball drop from a height of 1 metre, demonstrating their resilience to cracks and scratches.
PPI: How have connecting systems (cable connectors, etc.) been improved to give better ease of installation to OEMs?
HO: Poka-yoke connectors to avoid incorrect wiring and keyed custom connectors to facilitate ease of wiring are some of the methods we are implementing in all future development.
Some ports, like Ethernet, have de-facto pinout standards, but otherwise it is generally required and expected by customers to keep the pinouts and port positions the same for migration to new platforms, as it requires little effort on the OEM side.
PPI: How has a greater number of sensors/improved sensing technology helped to drive a better HMI experience? Are we reaching the point of information overload due to the number of data sources?
HO: Sensing technology hasn’t helped drive a better HMI experience, except for the increased speed and quality of the information exchanged. More inputs to these sensors for different use cases have made it easier to automate certain operations, but from an HMI point of view, it has not changed much except that you can see these sensors’ information on the cluster.
The amount of information the operator expects and what is typically provided is well balanced. However, too much information or too many notifications can distract an operator, potentially introducing safety concerns. Even if there aren’t inherent environmental hazards, it can still be an overwhelming experience for the operator to manage information on the screen while performing tasks with the machine.
PPI: Some Tier companies have demonstrated holographic switches, which offer the dual benefit of being visible in low-light situations and not affected by dust. Is it likely that these will gain more traction in the market?
HO: The use case certainly makes sense, but it must be validated by more OEMs and end users to gauge its future potential.
PPI: Beyond integration of larger screens into the instrument panel – and particularly with backhoe loaders - would it be possible/feasible to have a series of screens which are mounted on the operator seat and would rotate with the seat to support operation of machinery to the front and rear of the machine?
“The amount of information the operator expects and what is typically provided is well balanced. However, too much information or too many notifications can distract an operator.”
-Herman Oberoi, Danfoss Power Solutions
HO: Yes, this is possible, and certain applications could benefit from it. In fact, we are already seeing some integration of displays in armrests.
PPI: It’s possible that in the future, alerts could be displayed on window glass – would this not be considered potentially hazardous due to the notification blocking the driver’s view?
HO: What information is displayed on the window screen and how it’s displayed determines if it adds value. It may be more convenient and safer, in the case of critical alerts, to see information displayed within the operator’s line of sight. In some high-end passenger cars, for example, navigational directions displayed in a contextual way make it easier for the driver to keep looking out of the window while using the information to take the necessary steps. While this example doesn’t fully translate to the off-highway industry, if there’s a frequent need to look away from the window to get information from a display, that could become a larger safety concern than translucent graphics blocking the operator’s view. If the information becomes a distraction, it should remain on a display.
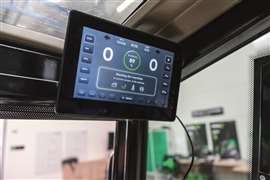
PPI: When it comes to using screens in off-highway machines, will it be possible to avoid displays which show “data for data’s sake” – showing information simply because it’s possible, not because it’s worthwhile for the operator.
HO: This is the goal in most, if not all, information display applications. The art, then, is to make it lean from a user point of view, by showing and clustering useful information in a way that makes sense, is easy for the user to act upon, and avoids unnecessary distractions.
Ultimately that power rests with the machine manufacturer. Displays within machines aren’t just monitors; they are small computers with processing power and display capabilities. Suppliers like Danfoss provide these programmable displays to OEMs, who then use C code, the display manufacturer’s graphics editor, or an open-source application to determine what information to display on the screen and how to arrange it.
Interestingly, it takes an incredible amount of time to develop the graphics for these machines, especially new machines with larger displays. Close to half the machine’s development time is spent just on the display graphics, while the other half is spent developing machine applications for the hydraulics, steering, and all the component interactions. Even though the display is a small part of the machine, it’s a huge part of the development work. For that reason, Danfoss is trying to standardize development by using widgets, either through our own dashboards and graphical editors or through the use of open-source editors with more libraries.
PPI: Will screen-based info tech (of any form) become redundant as more machines become remotely operated or autonomous?
HO: We’re a long way from fully-autonomous machines where the operator’s need for screen-based information becomes obsolete. There are safety considerations that require an operator either in the cabin of the machine or nearby, and both of these cases would need an HMI cluster to monitor and oversee the machine, even if fully autonomous.
CONNECT WITH THE TEAM

