Making concrete and asphalt more sustainable
12 August 2021
Ian Cameron reports on how companies supplying materials are continually refining their efforts, as the construction sector continuously embraces the green agenda.
Companies involved in the provision of construction materials are being forced to become more technologically advanced, as the sector is increasingly under pressure to ensure that it uses the most environmentally-friendly materials – especially asphalt and concrete.
The use of materials that have been reclaimed has strengthened over recent years as businesses become more aware of their environmental obligations and the realisation that there are significant advantages linked to using recycled aggregates.
A 2020 report from the University of British Columbia (UBC) School of Engineering on the Okanagan campus claimed that recycled concrete can, in some cases, outperform conventional concrete.
Researchers at the School of Engineering conducted side-by-side comparisons of recycled and conventional concrete within two common applications, namely a building foundation and a municipal sidewalk. They discovered that the recycled concrete had comparable strength and durability after five years of being in service.
Given that previous studies have estimated that waste materials from construction and demolition contribute up to 40 per cent of the world’s waste, the case for recycling becomes ever stronger.
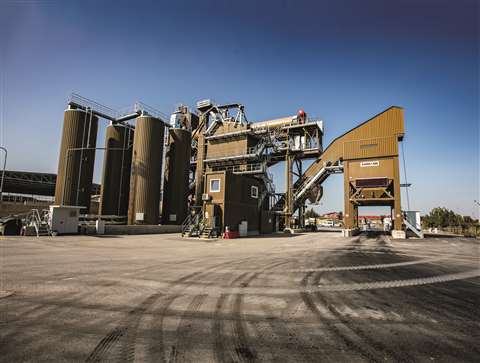
How is asphalt changing?
According to Ammann – which supplies mixing plants, machines and services to the construction industry – the production of asphalt mixes for the construction market is changing quickly. This highlights the trend to use as much recycled material as possible, which reduces the environmental impact of asphalt production.
Ammann ABP 240 HRT was recently purchased by Czech Republic company Pražská Obalovna Herink s.r.o. (POH). Approximately 90% of POH’s mix is delivered to its two parent companies, with the remaining 10% used by individual customers.
Roman Kadlec, plant director for POH, explained, “We acquired the HRT plant with the expectation that it is more environmentally friendly, has greater reliability and is a more energy-efficient operation.
“Another deciding factor was the ability of the plant to produce asphalt mix with higher amounts of RAP [Recycled Asphalt Pavement] as well as mastic asphalt.”
The machine’s current production is mainly on the modernisation of a highway near Prague, the capital and largest city in the Czech Republic. The ABP HRT features an RAH100 drum, which provides indirect heating of RAP and means that the recycled material does not come into direct contact with the flame.
Ammann pointed out that the binder is not degraded and there are not high emissions, therefore it is possible to produce asphalt mixture consisting of 100% RAP.
POH plans to produce a wider scope of asphalt mixtures containing a higher amount of RAP, although the plant recently produced a mix with 90% recyclables.
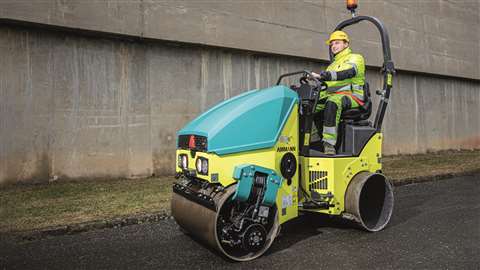
Reducing emissions in construction
Jan Thomschke, commercial manager and customised special orders manager with the Ammann Group, informed International Construction that there is always pressure to reduce emissions.
He said: “Because a great deal of progress has been made, which of course is good news, it is challenging to find opportunities for further reductions.
“There also are some non-traditional types of emissions – noise, dust and odour – that are increasingly of concern as asphalt-mixing plants are located in commercial and sometimes residential areas.
“To overcome this challenge, firstly Ammann supplies technology that enables the use of biofuels. These fuels support climate protection and reduce dependency on mineral oil.
“Examples of these fuels are rapeseed and sugar cane. Tall oil, which is a waste product of cellulose sulphate production, can also be used.”
Thomschke added that Ammann technology allows the use of these renewable energy sources or, in some cases, converting a waste product into fuel. This conserves natural resources and puts less pressure on landfills.
The use of reduced-temperature asphalt as a road construction material is a well-established technology, which is part of the drive to reduce emissions.
For example, Tarmac – a sustainable construction materials, road contracting and building products business – offers ULTILOW, which is a range of warm mix asphalts for more sustainable road surfacing. ULTILOW warm mix asphalts are manufactured and supplied at lower temperatures than conventional hot mix asphalts.
Tarmac stated that, as a result, they offer significant reductions in carbon dioxide emissions of up to 15% and typically around 8% to 10%. They also deliver a range of site safety and productivity benefits.
UK-based construction materials group Breedon offers its Lower Temperature Asphalt (LTA) which, the company remarked, offers a range of benefits.
These include the fact that no specialist equipment is required, as it is installed in the same way as hot mix asphalt. The process does not involve water, so almost all bituminous hot mix materials can be produced at lower temperatures, from road bases to thin surface course systems.
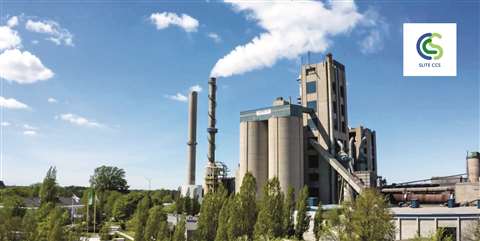
Construction’s effect on the environment
Building materials company CEMEX launched VIALOW a new range of low temperature, low carbon asphalts earlier this year.
The company pointed out that VIALOW uses a specially formulated bitumen additive to enable manufacture at up to 40°C lower than standard asphalt mixes. It is reported to produce up to a 20% reduction in embodied carbon emissions.
The company claimed that the lower temperature of the manufacturing process can also help to improve the long-term performance and durability of the asphalt. This is because a high temperature in conventional mixes leads to more oxidative hardening of bitumen than is seen in lower temperature variants.
Carl Platt, CEMEX’s director of asphalt, paving and building products for Europe, said: “With the launch of VIALOW, CEMEX aims to make it simple for customers to choose more sustainable and environmentally-friendly asphalts that have a lower embodied carbon, offset residual emissions and help drive vital change.”
He explained that this new range is designed to produce faster construction times, minimise disruption and reduce road maintenance costs alongside the added benefit of a carbon footprint reduction.
HeidelbergCement, a German multinational building materials company headquartered in Heidelberg, has announced its intention to upgrade its plant at Slite on the Swedish island of Gotland to become the world’s first carbon-neutral cement plant.
The installation at the Slite plant of HeidelbergCement’s subsidiary Cementa will be scaled to capture up to 1.8 million tonnes of carbon dioxide annually, which corresponds to the plant’s total emissions.
The use of bio-based fuels in the cement production at Slite will be increased in line with the group’s commitment to significantly raise the share of biomass in the fuel mix. The full-scale capturing of the plant’s carbon dioxide emissions is targeted by 2030.
HeidelbergCement is currently building what is claimed to be the world’s first full-scale installation for carbon capture at the Brevik cement plant in Norway, capturing 400,000 tonnes annually (or 50% of the plant’s emissions) from 2024 onwards. The company claim that the planning for the plant in Slite will benefit significantly from the experience gained at Brevik.
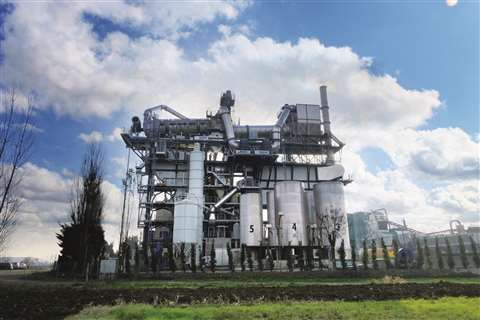
Eco-friendly features for Fayat
Luca Camprini, vice president of sales and marketing for Fayat Mixing Plants informed International Construction that the company “respects the environment” with regard to the production of asphalt.
He said: “When it comes to road pavement, the reuse of existing materials – and specifically of the milled material coming from road infrastructure pavements subject to wear – the ability to produce mixtures with reduced carbon dioxide emissions and energy savings are all essential issues for those who want to produce asphalt that respects the environment.
“This is also true for those customers choosing a continuous plant, requiring simplified transportation and installation, reduced cost of maintenance while relying on seamless quality, and for customers choosing a batch plant.”
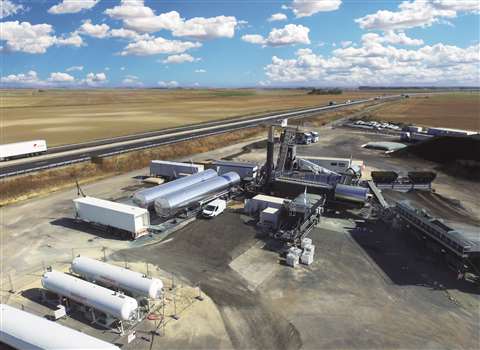
As an example of the company’s green credentials he cited its Marini-Ermont RF400 Highway hypermobile asphalt plant. Its environmentally-friendly features include the machine’s low height, which enables it to hide behind small trees.
Its extreme mobility allows it to be as close as possible to sites. There are also very low emissions, partly due to the use of clean fuel (LPG) instead of heavy fuel, and features – such as the elimination of fuel oil in favour of gas fuel – that remove the risk of soil pollution.
A leading company in this field is German-based Benninghoven, part of the Wirtgen Group, which is a world-leading supplier of asphalt mixing plants, machines and services to the construction industry.
Matthias Lenarz, team lead bitumen systems with Benninghoven, said, “Reduced-temperature asphalt offers financial benefits, as these mixes require much less energy to produce.
“Lower energy consumption always means a reduction in emissions, especially CO₂ emissions and potentially significant savings for customers. It is vital that the industry continues to be increasingly environmental conscious, which is why reduced-temperature asphalt ranks high on the agenda of authorities worldwide.”
A temperature reduction of 30 °C alone saves 0.9 litres of heating oil (or a fuel equivalent) per ton of finished asphalt, according to the German Asphalt Association.
Lenarz explained: “A daily production rate of 2,000 tons of mix corresponds to a savings of 1,800 litres of oil – or up to three-quarters of the energy required to heat a single-family home for an entire year. In addition, this corresponds to a reduction in CO₂ emissions of 6,000 kg per day.
“The figures that can be achieved in the real world are even higher, primarily because the reduction in temperature often reaches 50 °C or more.”
CONNECT WITH THE TEAM

