How one C&D waste specialist has doubled its recycled materials production
18 October 2024
CCC Waste, a United Kingdom-based waste management company, has doubled its production of recycled sand and aggregates, following the installation of a new wet processing plant from CDE.
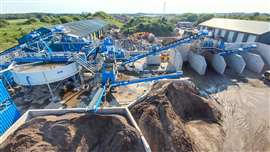
Established in 1986, CCC Waste is one of the largest recycling operators in the North-West of England, managing a range of construction and demolition (C&D) waste.
The company, which operates from a 35-acre site in Kirkby, had previously dry-processed over 15,000 tonnes of material a week, but was unable to extract sand and anything less than 50 mm in size was going to landfill.
CCC Waste invested in the new CDE plant to help it improve its previous dry crushing and screening methods, which were particularly impacted during winter months when feed materials were damper and therefore more difficult to process.
Sean Munro, Director at CCC Waste, said: “It was evident that many of the downstream challenges around product quality, specification, and waste to landfill volumes, to name a few, were stemming from inefficiencies in the dry crushing and screening process.”
He added: “We wanted to reduce the volume of material being sent to landfill, provide effective circular economy solutions for our customers, and increase our production volumes.”
Described by CDE as “flexible and responsive”, CCC Waste’s plant comprises a R4500 primary scalping unit, the AggMax scrubbing and classification system - which removes organic material and other contaminants, and the EvoWash sand washing system complete with CDE’s patented Infinity dewatering screen.
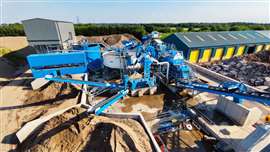
Capable of processing up to 200 tonnes of material an hour, other key features of the plant include the AquaCycle thickener for primary stage water management and a Filter Press, which recycles up to 95% of process water for recirculation and reuse.
According to the waste management specialist, the installation of its CDE plant, which was commissioned last year, has enabled it to increase its output to 30,000 tonnes of washed recycled materials per week, and to produce nine graded products, ranging from 0-2 mm and up to +80 mm oversized, as well as filter cake by-product.
Sean said: “The plant has exceeded our expectations and doubled the size of our aggregates business. Our customers are very happy with the material we’re producing, which is being supplied to many large developments in the area.
He added: “...we’re even collaborating on a project to develop a concept brick from the filter cake by-product that requires no heat to cure and is low energy.
“The idea is scalable, sustainable, and really aligns with our long-term environmental vision. It means we’re diverting 100% of our construction, demolition, and excavation waste from landfill.”
CONNECT WITH THE TEAM

