Global expansion of wind turbine construction
16 August 2021
As the expansion of the global wind industry accelerates, new turbine erection equipment and techniques are being rapidly adopted. Christian Shelton reports.
With the global push to meet climate change goals there has been a corresponding increase in wind farms being built, some on a spectacular scale. In February 2021, for example, plans to build a KRW48.5 trillion (US$43.2 billion) offshore wind farm by 2030 were revealed by South Korea to help the country become carbon neutral by 2050, which will be the world’s largest offshore wind farm.
In North America the increase in the number of wind farms being built is continuing to be brisk.
Buckner HeavyLift Cranes salesman Jay Breitbach commented, “We are expecting 2021 to be another blockbuster year for wind power construction.”
The company stated that its four most in-demand cranes for wind turbine installation are its Liebherr LTR 1220, LR 1300SX, LR 1600/2 and LR 11000, of which it has at least 20 units of each model.
Buckner stated that he anticipates growing demand for its Liebherr LG 1750 cranes, particularly for projects located in complex, forested terrain which is not asconducive for a crawler crane. Out of those cranes, Buckner identified the LR 11000 as the premier main installation crane for the USA wind power market.
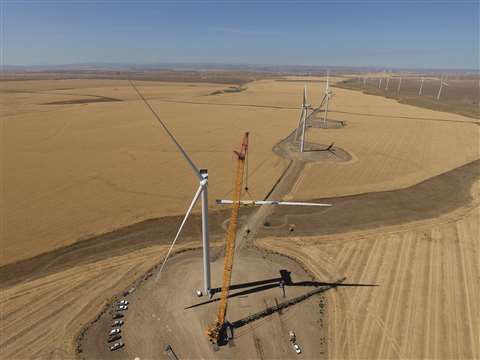
Meredith Williams, executive vice president of operations for Buckner, explained, “What sets the LR 11000 apart is its ability to simultaneously deliver high lifting capacity and high hook heights, with a simple main boom and fixed jib configuration and without a derrick.
“Similar to the LR 1600/2, it has excellent wind speed limits and impressive ground bearing pressure with its wide track pads.”
With its main boom and fixed jib, it has installed nacelles weighing 170 to 200 US tons (154 to 181 tonnes) up to a hub height of 112 metres, while also installing smaller turbines up to a hub height of 122 metres. It does things no other crane in the market can do and is well-positioned to continue increasing its market share.
This year Buckner’s cranes will be constructing the first Vestas V162-5.6 Enventus wind turbines in the United States, at a project located in north-central Texas and also GE’s new Sierra model at a project in New Mexico.
Crane and rigging service provider Barnhart is also breaking new ground in the United States. In conjunction with Indian company Windcare India, Barnhart introduced a craneless technique for wind turbine blade bearing exchange work for the first time in North America in Abilene, West Texas, during the 2020 summer.
Barnhart claims that it was also the first time that this technique had been used on the particular turbine platform being serviced.
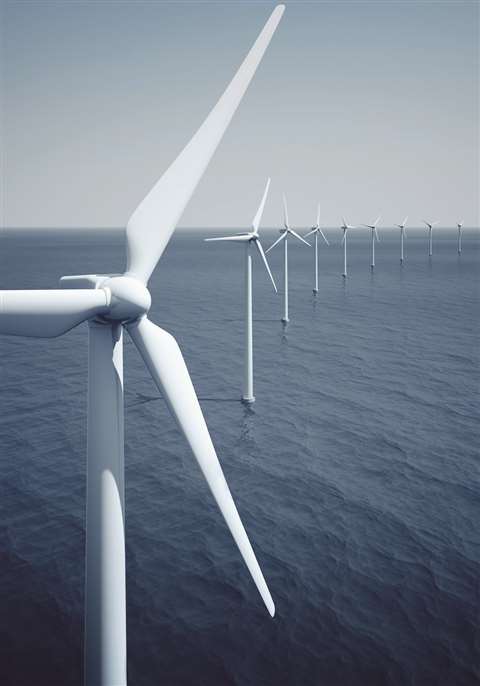
Controlling damage of wind turbine blades
Following the initial installation the system was tested on a blade from a different manufacturer. Unfortunately, due to this blade’s structural integrity the blade was damaged during the exchange.
In response Barnhart developed a modified procedure to use trailing edge and leading edge protection (or blade tacos).
The field team completed the project safely in two phases. The first phase lowered the damaged blade using the craneless system, with the modified trailing edge and leading edge protection. The second step then safely raised the blade using the same system after the repair was completed by a third-party.
Avoiding blade damage has also been a focus for Oklahoma-headquartered The Crosby Group (Crosby). The rigging, lifting, and load securement hardware specialist manufactures a range of lifting clamps designed for applications in the wind industry.
The company said that a common problem when handling steel plates with lifting clamps is that the clamping cam segment and pivot can leave an indentation in the material surface, known as marring.
The Crosby IP-branded standard and custom vertical and horizontal lifting clamps are designed to avoid this by reducing the height of the teeth of the cam segment and pivot.
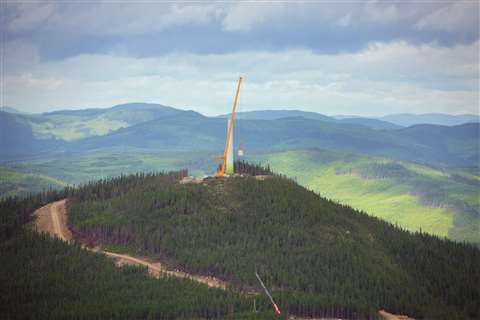
Another large crane rental firm carrying out a lot of wind erection work in the United States is the All Family of Companies.
Kevin Hileman, branch manager of Central Rent-a-Crane (Indianapolis, USA), a member of the All Family of Companies, said, “All Crane has been involved with many wind turbine projects in recent years.
“We have forged exceptionally close working relationships with all of the major wind contractors in America–Blattner Energy, Mortenson Construction, IEA Constructors, Wanzek and Fagen & Boldt.
“With this being the case, cranes of every type from the All Family of Companies have been on renewable energy projects of all sizes all over the country.”
One of the latest additions to the All Family of Companies’ fleet is the 800 tonne capacity Liebherr LR 1800-1.
Scott Jerome, branch manager of Dawes Rigging & Crane Rental (Kaukauna, Wisconsin, USA), a member of the All Family of Companies, stated, “This machine has unmatched versatility when it comes to wind applications.
“This is by having several wind-specific, mast-less configurations coupled with heavy and high lifting that can be done with its V-Frame derrick-suspended Vario-Ballast Tray attachment.”
“It has stronger load charts than close model competitors and offers ease of assembly and transport. Without question the rock star of our top out crane fleet is our Manitowoc MLC650.
“Its versatility from mast-less configurations for shorter height (80m to 90m hook height) wind turbines on up to the VPC-Max attachment allow this 717 ton (650 tonne) class machine to do work that, prior to its arrival in the marketplace, had to be done with much larger crawler cranes.”
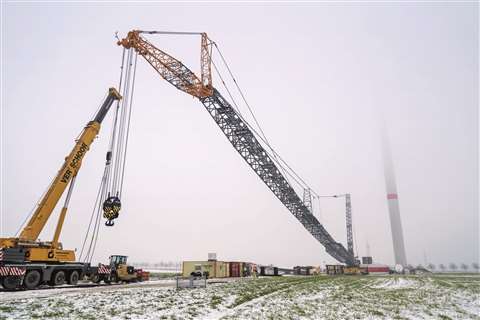
M. Verschoor, the crane contractor in the Netherlands, has bought a new Liebherr LG 1750 lattice boom mobile crane fitted with Liebherr’s new SX3 boom system. Liebherr claim that the SX3 delivers an increase in lifting capacity of up to 20 % with significantly higher wind tolerance compared to the original SX version.
M. Verschoor has been using the 750 tonne capacity crane to erect two Vestas turbines in North East Germany with hub heights of 170 metres.
M. Verschoor crane operator Johan Bezemer commented, “The crane with its SX3 boom enables us to increase our capacities so that we can erect very large turbines. Its 165 metre main boom and 12 metre jib gives us a lifting capacity of 127 tonnes, which is really enormous.”
With the lower section of the lattice boom having been extended to a width of 6m, the SX system now allows work to continue in wind speeds of up to 10 metres per second, or in some cases even 11.2 metres per second according to Liebherr, when compared to the earlier systems on the LG 1750 that were calculated on the basis of a maximum wind speed of 9 metres per second.
Hileman added, “The most telling effect of the new generation of wind turbines is that much larger cranes are required for the top out lifts. Cranes that just a few short years ago were used as the top out cranes are now being used as base or mid tower setting cranes.
“The larger top out cranes obviously require larger support cranes, and the more efficient these support cranes are, the better.”
This search for efficiency underpins all the choice of cranes and new equipment developments, so it will be interesting to see how this fast-changing sector evolves in the near future.

Belgium-headquartered heavy lift and transportation specialist Sarens is using a Demag PC 6800-1 pedestal crane to lift foundation piles for Fryslân wind farm in the Frisian part of Lake Ijsselmeer near Breezanddijk, the Netherlands.
Sarens is carrying out the work for Dutch global marine contractor Van Oord Offshore Wind. But because the lake is so shallow Sarens had to build a large floating platform with a shallow draft from which the crane could carry out the lifts.
The floating platform measures 62 x 53 metres, approximately half the size of a football pitch, and so has been nicknamed the ‘Sarens Soccer Pitch’.
Although the platform was technically large enough for a lattice boom crawler crane, Sarens decided to use the Demag PC 6800-1 pedestal crane as it was easier to set up given the unusual conditions and the 1,250 tonne class pedestal crane provided all the required performance.
The Demag PC 6800-1 was transported from its previous jobsite in Hungary to the Dutch coast, where it was subjected to technical checks before being set up. Due to the tight space conditions on the barge platform the setup was thoroughly planned.
The crane is now lifting piles, each weighing up to 250 tonnes and measuring up to 40 metres, directly from a transport ship and placing them in an upright position with the aid of a sheerleg. The pile is then moved into position and driven into the IJsselmeer’s lakebed.
Mart van Hoorn, Sarens project manager, explained, “We first pre-assembled the crane on the shore and then put together and tested the larger components on the barge. This way, we minimised the potential risks of assembly on the water and at height.”
CONNECT WITH THE TEAM

