Engineering the ultimate asphalt surface

Partner Content produced by KHL Content Studio
21 November 2024
Any major road construction project will come with complex challenges, including the management of traffic flow, space limitations, coordinating with utilities, the unpredictability of weather, and so on.
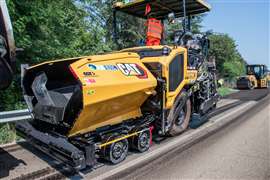
It’s therefore important to ensure complications arising from paving equipment are removed from the list of issues wherever possible.
From a technical perspective, the variables of asphalt paving mean keeping things constant can be key to a successful project – and that can mean anything from simple momentum to asphalt temperature, equipment uptime and materials delivery.
Settings and adjustments on the tractor and screed must be optimised, regular checks must be made to ensure the asphalt is to specification, and delivery logistics must be maintained in real time, to avoid situations in which pavers are kept waiting for material.
When these and other associated factors are out of alignment, as well as holding up proceedings, it will often result in an imperfect finish on the asphalt that is paved out.
Ahead of breaking ground, experienced road construction businesses will aim to simplify operations and processes; placing ever greater reliance on digital technology to do that. In fact, technology is shifting more from a ‘nice to have’ to a ‘must have’, in a sector struggling to replace the large number of retiring skilled operators.
With this in mind, road construction equipment needs to combine simplified processes with the sort of cutting-edge technology that can help less experienced crews deliver the quality finishes demanded by European highways authorities.
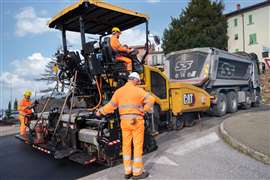
The construction equipment giant Caterpillar has been increasingly focused on this sector for a number of years and has released new paving machines and related technologies designed to answer these and other challenges of modern road construction.
Carriages and the paving train
Caterpillar recently updated its pavers range with four new machines, the largest of which is the AP555, which has an operating weight of 16,296 kg (steel track) and a paving range of between 2.55m to 5.0m, up to 7,64m with bolt on extension (with SE50VT screed).
The range of new machines covers all the undercarriage bases, with the AP400 being a wheeled model, the AP455 carrying the Cat® Mobil-Trac™ System (about which more later), and the AP455 being a smaller version of the AP555.
The new pavers are generally lighter than equivalent predecessor models and have enhanced hydraulic systems. As well as benefitting productivity, these improvements – along with a new design aimed at reducing the amount of material in front of the screed as it progresses – play a significant role in reducing fuel consumption.
The importance of optimising the uptime of road construction equipment cannot be overstated, given the chain-of-events nature of the business. If the paver has broken down when the truck arrives with the asphalt, then, not to put too fine a point on it, everything breaks down, right back to the aggregates and binder being loaded into the asphalt batching plant.
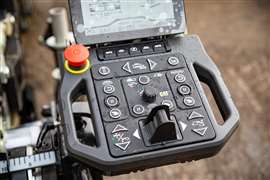
To this end, another important change, reflected across the new paver models, is the addition of VisionLink® Management Technology.
With VisionLink now as standard, supervisors can monitor the health of pavers and reduce unplanned downtime via critical alerts. Fault codes, fluid analysis and inspection due dates can all be displayed, while parts can be ordered and services scheduled, all within the platform.
The cutting edge of simplicity
It may seem incongruous to talk up the advanced technology available on pavers, having previously highlighted the shortage in skilled operatives, but Caterpillar says its on-board system is designed to simplify the asphalt paving process, potentially making the job easier for younger and less experienced road construction crews.
One such system available on the new pavers is Pave Start Assist, which records the functioning conditions of both the paver and the screed, including paving width, paving speed, tow-point position, etc.
Operators can create and save new profiles, retaining existing setup parameters that ensure constant performance across projects, and the ease-of-use options continue with hopper control functions, automatic auger and conveyor activation and a warm-up/clean-out mode.
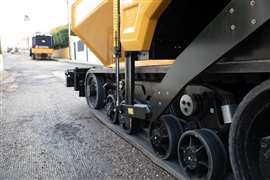
Cat Grade Control is also available on the new machines, allowing operators to set target depths and pave in automatic mode. The system offers real-time sensor feedback, ensuring smooth transitions when paving through challenging intersections or bridge approaches.
Tracks and wheels
Factors such as paving width, surrounding terrain and urban sensitivities will have a bearing on the optimum undercarriage for a paver, along with cultural working practice preferences, which can vary greatly throughout Europe.
While wheeled models tend to be faster and more manoeuvrable, tracked machines offer greater stability and allow for a wider paving area.
In particular, Caterpillar’s new AP455 and AP555 pavers with Mobil-Trac undercarriage could appeal to companies operating in urban environments, as they combine good travel speed (11km/h) and manoeuvrability, with enhanced traction. Their pivoting bogie system also allows them to smoothly overcome obstacles as they absorb irregularities in the terrain.
Labour-saving in paving
As much as equipment and technology can take the strain on a construction project, there will always be a need for manual labour in the process.
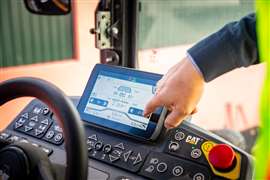
The new Cat pavers are designed to mitigate this where possible, even in the physically demanding area of manipulating the screed as the paver proceeds.
The latest machines have a slightly smaller auger diameter, which reduces the distance between the screed and the tractor, subsequently reducing the amount of material to be carried in front of the screed.
Add to this a new carriage design for the screed and symmetrical extenders and the view of the auger chamber is improved, allowing the operator to see and control the material flow from the walkway.
Caterpillar’s engineers have also developed new independent screed control panels, designed to give operators greater control of screed functions, including a dial for simple mix-height adjustment and a three-speed proportional extender control for a highly tailored delivery.
Considering a Cat? In Europe, Caterpillar has established an impressive network of 21 dealers, each of which is now offering paving machines equipped with Cat Product Link. This device wirelessly transmits data on working hours, location, fuel usage, general machine health and more, which customers are able to access via a laptop or mobile device. Product Link is API-enabled, meaning the data can be integrated into other systems, allowing businesses to keep track of crucial machine information, even across mixed fleets. Another potential benefit from the Caterpillar dealers is the Fuel Promise Program, which, simply put, says “Our machines’ fuel consumption should not exceed our promised value. If it does, Caterpillar will reimburse you the difference”. Given that fuel is one of the highest operating costs for any construction business, a promise like this from Caterpillar could prove the tipping point for anyone considering a paving machine investment. Also, the program is free to customers, with the only stipulation being enrolment in a 3-year service contract. |
Compaction in the ‘green zone’
Where ease of use and operator comfort used to be little more than an afterthought in road construction, they are now seen as central to improved productivity and the retention of skills, both of which are beneficial to the all-important bottom line.
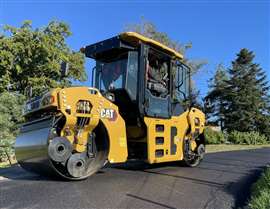
Caterpillar’s latest models of compaction machines – the CB7, CB8 and CB10 – also offer an enhanced operator experience, through a combination of engineering innovation and advanced digital technology.
As an example, operators can quickly access saved profiles that include settings such as speed, impact spacing, frequency/amplitude and water spray rates, greatly simplifying setup on the job and when moving between jobsites.
Simplifying operations through optimised performance is a win-win, which Caterpillar says it can deliver with a new system that shows operators when they are in the ‘Green Zone’ – in other words, they have matched the compactor’s travel speed, for the correct impact spacing.
A pressing need for tech
The pursuit of optimal compaction has led to the development of many of the digital systems on-board the latest Cat machines. Optional Compaction Control Technology, for example, allows operators to map asphalt temperatures and count machine passes, giving them confidence that attention is being given to the whole surface, even during nighttime operations.
The new CB7 and CB10 can also be equipped with split drums, to ensure the machines can manoeuvre seamlessly in tight spaces. Using this system, operators can rotate the outside half-drum faster than the inside, preventing any tearing or shoving of the asphalt while making turns.
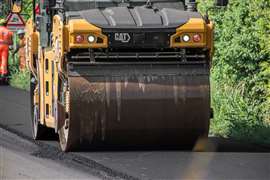
As with the Cat paver models, the new compaction machines have fuel economy benefits, largely through their ability to automatically modify engine speed, dependent on load requirements.
The CB10, for example, can deliver up to 10% better fuel economy with its Cat C3.6 engine and standard Eco-mode, compared with the previous model.
Attention to detail
Caterpillar’s paving division has been fine-tuning its range of road construction equipment in recent years, bringing the same cutting-edge technology to bear on pavers and compactors, as it has on its earthmoving and mining machines.
As well as a shift in body design, tending to make Cat machines more appealing to the European eye, the new models are serious contenders when it comes to making road construction projects quicker, more efficient and more profitable.
Caterpillar paving equipment update The latest pavers from Caterpillar are the AP400, AP455, AP500 and AP555. The AP400 paver is a wheeled model. The latest compactors available from Caterpillar are the CB7, CB8 and CB10. |
--------
All images courtesy Caterpillar
--------
This article was produced by KHL’s Content Studio, in collaboration with experts from Caterpillar
CONNECT WITH THE TEAM

