En-shoring safety: Modern advancements in shoring and scaffolding for deconstruction
25 September 2024
Aaron Denton, Executive Vice President at Tiny’s Demolition & Recycling, reveals how the company demolished the historic structure at 200 Broadway in Nashville, Tennessee.
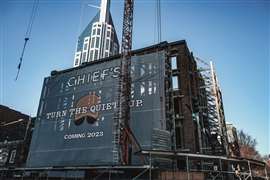
Worksites in urban areas with a high population density always present a specific set of challenges, but when located on a road where the daily footfall traffic can reach into the hundreds of thousands, the job of keeping people safe goes to a whole new level.
“I remember coming home and my wife would say: ‘Why are you so stressed?’”, recalls Aaron Denton, Executive Vice President at Tiny’s Demolition & Recycling, as he recalls the time he spent working on the company’s project at 200 Broadway Street in Nashville, Tennessee.
“I replied that it was because I didn’t want anybody to die, and she said: ‘Well, that’s being a bit dramatic,’” Aaron laughs.
“I repied: You don’t understand – on one side it’s our people, and on the other side it is thousands of people”.
In this case, ‘thousands’ of people is not an exaggeration.
Famed for its honky-tonk bars and live country music venues, Broadway Street in the Lower Broadway area of Nashville is the cultural and historical heart of the city.
Drawing over 16 million visitors each year, an average of 230,000 people walk down the famous street where the project site was located every day.
This meant that Tiny’s project to demolish No. 200 Broadway – a five-storey structure built in the 1880’s – required significant planning.
“We were in the design phase way before the project was even awarded,” says Aaron.
“It was probably a couple years before, when we started to talk about the process and how we were going to do the works with the engineer and the general contractor.
“I swear it was like 400 meetings in total. It really felt like every day there was a meeting or some other discussion about it.”
The project: 200 Broadway Street
But the high level of pedestrian traffice was not the only challenge presented by the structure.
For Tiny’s and its project partners, the selective demolition of the five-storey structure was unlike any other demolition project they had done before.
Built in the 1880s, the most demanding aspect of the project was that the city’s Historical Commission insisted on retaining the building’s two street-facing façades.
With this being the case, the challenge for Tiny was to keep the exterior walls facing Broadway and 2nd Avenue standing, while removing the structure’s remaining elements.
This work required the demolition of the roof and floors along the building’s west wall, and half of the north wall to maintain the structural integrity of an adjoining building, which was occupied throughout the project.
Exoskeleton shoring
Fortunately, modern advancements in shoring and scaffolding meant that Tiny’s team was able to put together a highly technical plan that incorporated the use of an exoskeleton shoring system, usually reserved for bridge support applications.
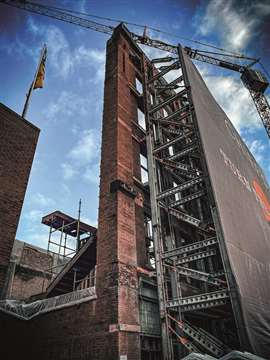
Requiring its own rebar-enforced concrete foundations, the exoskeleton shoring took four weeks to erect.
While the exoskeleton supported the walls that were to be retained, the remaining walls had to be removed by hand, brick by brick.
“We were literally pulling bricks off by hand because the mortar was so old,” says Aaron, adding that they were unable to even use power tools because the mortar was in such poor condition.
Additionally, 80% of the bricks had to be salvaged for reuse on the building’s redevelopment.
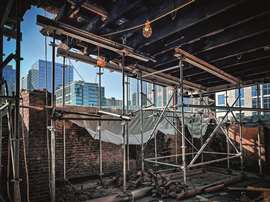
By incorporating swing stages, Tiny’s was able to keep their personnel safe and control the speed of demolition.
The contractor also used a tower crane and, by live loading materials into a skip pan, they were able to transfer the materials into a dumpster, which could be lowered to the ground for transport off site.
Additionally, interior post shoring was installed to free the floors from the walls once the exterior walls dropped below the pocket joists to prevent the floors from collapsing.

Onsite challenges
A major challenge that developed during the initial demolition phase of this project was that once the parapet wall on the roof was removed, the roof structure started to move, creating a major hazard for the team on the swing stages.
“You can go through the whole planning process, you can go through the steps, the checklists and all these things... But when you’re dealing with a 150-year-old building in downtown Nashville, things change.”
Utilising daily safety and structural inspections, the contractor was able to maintain a safe working plan while the roof structure was removed. But that wasn’t the only challenge Tiny’s team encountered.
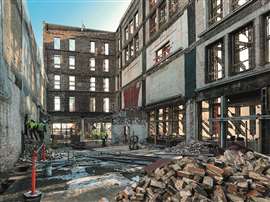
Aaron reveals: “We would take some of the wall down and then we’d take down the floor and then we’d go back to doing the wall and another floor, and so on.
“But with all the weight and the shoring, when we removed more of a wall, the floor would all of sudden start to kick out, because of all the pressure. So, we had to stop work and re-evaluate this situation.”
Once the above ground structure was removed, the team was then tasked with digging the solid limestone foundations to 12 ft (3.5 m) below grade.
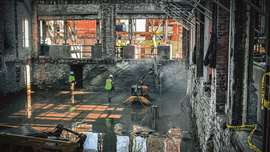
The contractor utilised Brokk demolition robots with drill attachments and chipping hammers to break the limestone into smaller rocks, which were used to build a ramp by which other equipment and material was transported into and out of the basement.
According to Aaron, it was the daily and weekly meetings with the project’s senior leadership team, engineer and third-party consultants, that ensured arising issues could be mitigated and the work successfully and safely completed.
CONNECT WITH THE TEAM

