Dismantling the Gerald Desmond Bridge: How Kiewit Infrastructure West did it
16 January 2025
Spanning five decades of service, the Gerald Desmond Bridge was deconstructed in a groundbreaking US$28 million project. Through advanced engineering, collaborative planning, and a focus on sustainability, the demolition achieved zero environmental incidents, repurposed over 100,000 tonnes of materials, and set a new benchmark for the industry.
The demolition of the Gerald Desmond Bridge, spanning the Long Beach Inner Harbor Back Channel in California, marked a significant achievement in collaborative engineering, sustainability, and technical innovation.
Completed in September 2023, four months ahead of schedule and $3 million under budget, the project stands as a model for environmentally conscious and cooperative demolition practices.
Project Overview
The Port of Long Beach (POLB) awarded the $28 million demolition contract to Kiewit Infrastructure West Co. in July 2021. Originally constructed in 1968, the bridge was a vital transportation link, supporting trade and travel for over five decades.
Spanning 1,566 metres (5,138 feet) in total, the bridge consisted of a continuous steel truss and steel plate girder structure. It comprised a 321-metre (1056-foot) main channel crossing that included a 125-metre (410-foot) suspended main channel span, two 18-metre (59-foot) cantilever arms and two 80-metre (263-foot) anchor arms, which added significant complexity to the structural system.
The bridge was flanked by approach structures measuring 691 metres (2,268 feet) and 552 metres (1,813 feet), with a total of 29 spans. These were constructed of steel plate girders up to 2.5 metres (8.33 feet) deep and 67 metres (220 feet) long.
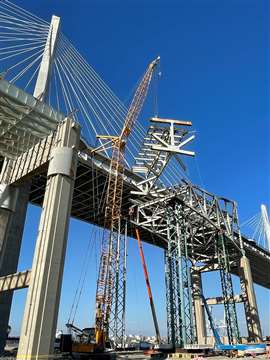
These elements required meticulous planning during demolition to ensure stability and safety, particularly during the removal of the 3.18-million-kilogram (7-million-pound) suspended span.
The demolition project encompassed the removal of the entire structure, including 33 reinforced concrete piers ranging up to 42 metres (138 feet) in height. All demolition work had to be carried out while maintaining uninterrupted operations at adjacent port facilities, including active shipping lanes, a railroad, and underground utilities.
Additionally, the bridge’s location in a bustling industrial hub required careful coordination to minimize disruption to tenants, businesses, and public infrastructure.
The Gerald Desmond Bridge posed unique engineering challenges, as its structural steel was coated with lead-based paint, necessitating stringent environmental and safety protocols during removal.
The bridge also featured a 20.6-metre-wide (67.5-foot-wide), 23-centimeter-thick (9-inch-thick) concrete deck, contributing to the complexity of dismantling and material recycling.
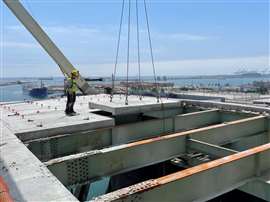
The project, which had a workforce of 55 people at its peak, was executed in three main phases:
1. Strengthening and removing the main channel crossing structure, which involved reinforcing the suspended span with temporary bracing before it was safely lowered using strand jacks. This step ensured the stability of the structure and minimized risks during the removal process.
2. Dismantling the approach concrete deck and steel superstructure, which required careful sequencing to avoid disruption to the active shipping lanes and nearby infrastructure. Advanced cutting and lifting techniques were employed to handle the heavy components efficiently.
3. Demolishing the land-based piers to grade, involving the use of precision-controlled explosives and heavy machinery to break down the reinforced concrete structures. This phase was completed with extensive dust suppression measures to meet environmental compliance standards.
This ambitious undertaking required a blend of advanced engineering, innovative demolition techniques, and close collaboration among all stakeholders to ensure its success.
Sustainability and Recycling Efforts
While sustainability was a primary focus, the project team also encountered several complex challenges that required innovative solutions to maintain their environmental goals.
Sustainability was at the forefront of this project. The team successfully recycled 100% of the materials generated during demolition, showcasing a commitment to environmental stewardship and resource conservation. This impressive feat included:
Steel: A total of 15,169 tonnes of structural steel was salvaged and transported to SA Recycling in Long Beach. This material was processed and reintroduced into the manufacturing supply chain, reducing the need for virgin steel production and its associated environmental impacts.
Concrete: Approximately 68,000 tonnes of concrete was crushed at a nearby POLB facility using advanced processing equipment. The resulting aggregate was repurposed for future POLB infrastructure projects, significantly reducing waste, and lowering the carbon footprint associated with transporting and sourcing new materials.
Soil: Over 22,063 tonnes of soil was carefully repurposed for both on-site applications and stockpiling at off-site POLB facilities. This approach ensured the soil’s usability while preventing unnecessary landfill contributions.
In total, 105,232 tonnes of materials were diverted from landfills, setting a new benchmark for large-scale demolition projects.
The recycling processes not only minimized waste but also reduced the environmental impact by conserving natural resources and cutting greenhouse gas emissions associated with material production.
The project’s focus on sustainability extended beyond material recycling. Throughout the demolition, the team implemented strict environmental monitoring protocols to ensure compliance with air and water quality standards.
These measures included dust suppression systems and runoff containment strategies to prevent contamination. Additionally, the lead-coated steel required careful handling and processing to eliminate risks to workers and the surrounding community.
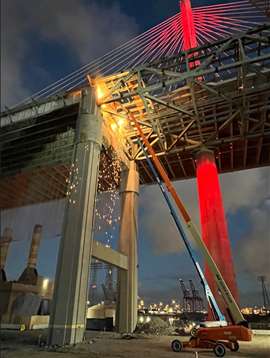
By adhering to these stringent standards, the project maintained zero environmental non-compliance incidents, underscoring the team’s dedication to eco-friendly practices.
The methods used during the project, such as the precise lowering of the suspended span, further contributed to its sustainability.
Not only did they minimize the impact on the busy waterway but they also reduced the energy and resources typically required for piecemeal dismantling. These efforts demonstrate how engineering ingenuity and environmental responsibility can work hand-in-hand to achieve outstanding outcomes.
Key Challenges and Solutions
Overcoming these challenges was only possible through close collaboration among all stakeholders, which became a defining feature of the project’s success.
Suspended Span Removal: Kiewit, working with its partners Somerset Engineering, McElhanney, Kiewit Engineering Group and its lowering subcontractor Barnhart Crane and Rigging, lowered the bridge’s 125-metre (410-ft), 7-million-pound suspended span intact, using 1022-tonne strand jacks and placed it onto a barge.
Execution of the lowering operation was closely planned, coordinated, and rehearsed with POLB and its tenants, whose shipping schedules would be impacted during the channel closure. The method, which required over 100 individuals to carry out, successfully minimized environmental and operational impacts by reducing the channel closure duration from 48 hours to 18 hours.
Environmental Protection: The bridge’s lead-coated steel required careful handling to prevent contamination. Air and water quality standards were rigorously upheld throughout the project, with zero environmental non-compliance incidents reported.
Proximity to Active Operations: Demolition occurred over and adjacent to operational port facilities, including an active shipping channel, railroad tracks, and underground utilities. Coordination with stakeholders ensured minimal disruptions, including night and weekend work to accommodate terminal schedules.
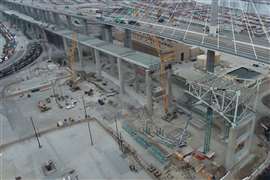
Collaboration and Communication
Collaboration among multiple stakeholders was pivotal to the project’s success. Key contributors included POLB, tenants, contractors, and regulatory agencies.
The project team established strong relationships through informal site walks, weekly coordination meetings, and formal partnering sessions.
These efforts facilitated proactive problem-solving and aligned goals, such as minimizing impacts and maintaining safety standards.
Industry Recognition
In recognition of these efforts, the project was shortlisted for the Collaboration Award at the 2024 World Demolition Awards. This nomination highlights the project’s success in fostering effective partnerships among various stakeholders, including the Port of Long Beach, Kiewit Infrastructure West Co., and multiple regulatory agencies.
The collaborative efforts were instrumental in completing the project ahead of schedule, under budget, and with a commendable safety record. The industry’s acknowledgment of the Gerald Desmond Bridge Demolition underscores its status as a benchmark for future infrastructure projects, particularly in terms of collaboration, innovation, and sustainability.
Technological Integration
Advanced digital tools were employed to optimize planning and execution:
LARSA 4D: Engineering modelling and analysis.
Enerpac Smart Box: Management of strand jacks.
Telematics: Equipment usage tracking.
3D Modelling: Tools like Sketch-Up Pro and AutoCAD enhanced crane pick planning.
EverCam: Documentation and project video recording.
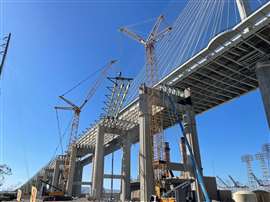
Outcomes and Achievements
Safety: The project achieved 136,613 person-hours without a single OSHA-recordable injury. Subcontractors also maintained a recordable-free safety record, reflecting the rigorous adherence to health and safety protocols.
Completion: Four months ahead of schedule.
Cost Savings: Over $3 million saved.
Environmental Stewardship: Zero non-compliance incidents and 100% recycling.
Stakeholder Satisfaction: Enhanced relationships and operational continuity.
Recognition: The Gerald Desmond Bridge Demolition project has garnered significant attention within the demolition and recycling industry for its exemplary execution and collaborative approach.
The project received the 2024 Associated General Contractors of America Marvin M Black Excellence in Partnering and Collaboration Award, and was shortlisted in the Collaboration category at the 2024 World Demolition Awards.
The collaborative efforts were instrumental in completing the project ahead of schedule, under budget, and with a commendable safety record. The industry’s acknowledgment of the Gerald Desmond Bridge Demolition underscores its status as a benchmark for future infrastructure projects, particularly in terms of collaboration and sustainability.
CONNECT WITH THE TEAM

