Construction hoist use is lowering labor costs, driving adaptation
10 January 2023
Fewer construction projects are passing over efficiency opportunities as rising wages and scarce labor, high materials costs and poor availability, erratic energy costs and corporate commitments to reduce carbon footprint challenge building completion. Many contractors are expecting sales and staffing levels to climb until at least May with stable profit margins. The conditions are creating demand for construction hoists.
Construction hoist market conditions
“Improving the logistical vertical transportation requirements on a project to move personnel, materials and equipment is becoming more and more a need for all clients, developers, planners and contractors in the construction industry as they all drive greater level of sustainability and efficiency,” says Cameron Reid, sales director with Alimak Group’s construction division. “We are encountering more and more complex facade modules, modular building units, prefabricated pods, heavy plant, heavier facades, etc., that are driving [us] to develop new accessories, applications and vertical access solutions.”
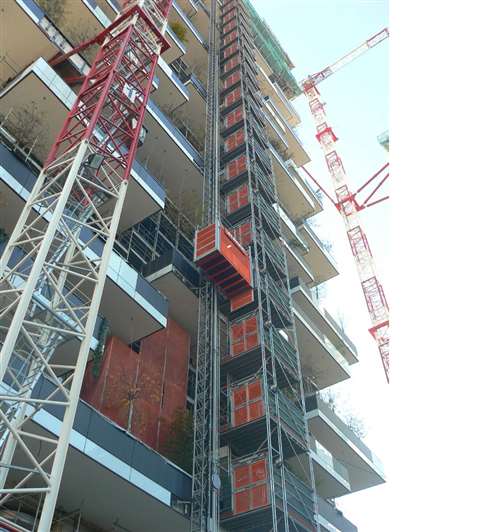
A 200-hundred or 300-hundred-foot project will use a construction elevator. Studies show conclusive safety and economic advantages of using elevators at this height. Today, construction teams are asking, “What is the minimum height where these same advantages can be realized? Is it a three-story building; eight; 10?”
Consider this construction-elevator cost analysis laid out by the Scaffold & Access Industry Association.
Assumptions:
- An eight-story structure requires an 80-foot stair tower or elevator and for eight months
- Thirty laborers, making an average of $50 per hour with benefits, need access to the structure
- Each laborer makes five daily round trips from grade to height
- Each trip takes approximately twenty seconds per floor
- The cost equation can be scaled to smaller buildings and reduced load on the building by substituting transport platforms for elevators.
“I have yet to meet a single general contractor who wouldn’t want to save 46% on anything, and this study merely represents the economic savings in simple climb time,” writes Paula Manning, of Century Elevators, in this comparison. She says these “additional benefits exist with the utilization of a construction elevator:”
- Productivity increases as workers get to their work site faster and without the need for recovery time after a climb.
- Riding an elevator eliminates the basic wear and tear on a worker’s body caused by carrying heavy tools upstairs.
- More-frequent inspection of the work by supervisors is possible due to easy access to various jobsite levels.
- There is less demand for expensive crane time as trades can move material with the elevator.
- More efficient stocking of floors.
- Improved project schedule.
Efficiency fitting smaller projects
The 15-story Virginia General Assembly Building in downtown Richmond had no internal elevator, so remodeling work could progress only as fast as a hoist could feed the job.
Scaffolding Solutions chose a Scando 650 Dual Hoist system with 7,100 pounds of capacity. The buck hoist lifted all the workers, tools, and materials to each floor.
Safety was paramount for all parties to the construction team. The chosen hoist included:
- Magnetic and electronic interlocks to prevent doors from opening while the hoist was in motion
- Pre-programmed landing locations for each floor
- Loading doors that automatically locked when the hoist left the ground
- Doors that could only open from the inside while the hoist was off the ground
Two enclosed cars operated independently on either side of a central mast, allowing general contractor Gilbane to easily maintain productivity.
Setting up two construction hoists to work at the same time on the same mast is becoming more common. Operating two different rack and pinion lifts on the same mast saves money and time for the operator and increases construction capacity.
“Having a dedicated material car while still being able to move personnel floor to floor was a huge benefit,” says Danny Dunbar, project manager for Scaffolding Solutions.
Hoists do more with fewer people
The scale of construction’s labor shortage is pinching productivity on all shapes of vertical construction. The Associated Builders and Contractors developed a model that forecast last February that the construction industry will need to attract nearly 650,000 additional workers on top of the normal pace of hiring in 2022 to meet the demand for labor. As of November, industry employment had risen by just 248,000 over the previous 12 months.
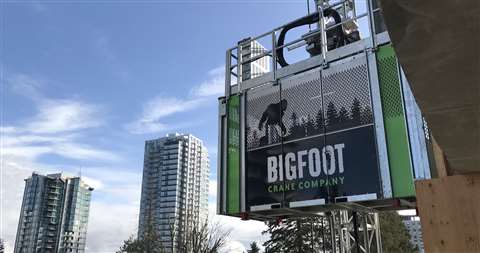
“The use of mast climbers and hoists is advantageous in this situation,” says Corinne Dutil, sales director at Fraco Products, “Because if teams are smaller when starting a project, these units increase productivity, speed, but also satisfaction of the workers.”
The strength of this return on investment in hoists is pushing back the limits of the equipment.
SafwayAtlantic recently completed the tallest hoist on a common tower and the world’s largest continuous rack and pinion hoist for a six-car construction complex for construction of the Central Park Tower. Located on Manhattan’s “Billionaires’ Row” and overlooking Central Park, Central Park Tower is the highest residential tower in the world and the second tallest building in New York City.
The common tower made from shoring and scaffolding components decked at each entry level for access reached the 99th floor, a world-record height of 1,515 feet 6 inches. To maximize labor productivity, a Hydro Mobile mast climber positioned above the hoist cars improved scheduling efficiency and eliminated interference between construction crews and tower-erection crews.
Rigging for more capacity
“There are many new materials being use in construction, and that creates new markets for mast climbing work platforms and hoists to be used in,” says Dutil. “New types of application create various opportunities.”
To carry huge glass-and-steel curtain wall panels for the façade of the new 60-story JPMorgan Chase headquarters in New York City, SafwayAtlantic worked with Raxtar to design two dual-mast hoist cars that measure 25 feet long by five feet wide by nine-and-a-half-feet high. These longest hoist cars in the world can carry loads of up to 10,000 pounds at speeds up to 300 feet per minute.
To boost efficiency, Designed Access’s EZ call system provides call-to-floor buttons. A loading dock television display shows hoist location at all times, and cloud-based software books hoist times to reduce downtime on the project.
Innovation to match façades
Inventive façade designs are driving hoist innovation to improve construction efficiency. For example, two Alimak passenger and materials hoists adapted to the varying positions and dimensions of terraces on the outside of the Bosco Verticale skyscrapers in Milan, Italy. The terraces became home to more than 900 trees.
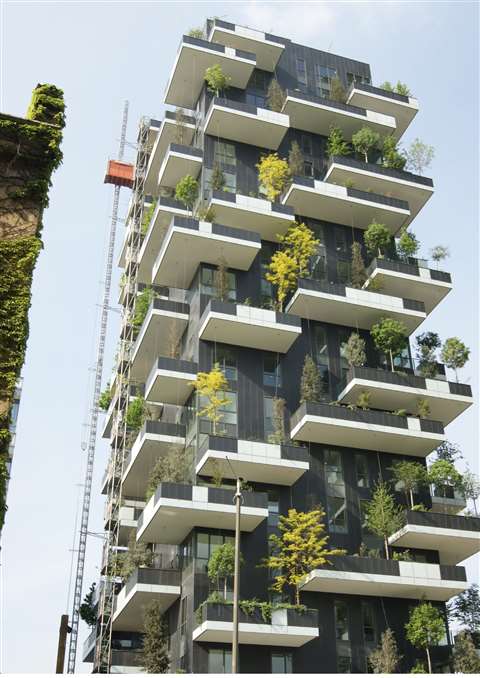
The first Alimak Scando 450 hoist had a 262-foot (80 m) lifting height and 17 landings. The second hoist reached 367 feet (112 m) and had 25 landings. General contractor Colombo Costruzioni collaborated with scaffolder ACG 5 to devise a landing solution on all floors that was easy and fast use.
Alimak’s ALC-II control landing system increased hoist efficiency, reducing waiting times at landings and optimizing loading and unloading. The job’s third big access challenge was to increase hoist uptime. The Alimak A3 remote monitoring system sent activity reports to jobsite engineers to avert downtime and keep maintenance on schedule.
The recession mystery
Perhaps the economy will affect the shape of the construction hoist market in 2023 most. For now, work volume looks strong well into mid-2023 but even with much of the recession noise having died down now that the election is over, the view of 2023 construction economy is murky.
The Associated Builders and Contractors’ Construction Backlog Indicator increased in November to its highest level since the second quarter of 2019.
“The rise in backlog is remarkable and unexpected,” said Associated Builders and Contractors Chief Economist Anirban Basu. “A number of contractors have been reporting that their backlog has risen rapidly over the past three months, which is counterintuitive given the pervasive view that the broader economy is headed into recession.”
Backlog improved sharply for contractors in the commercial and institutional work category, and health care-related construction emerged as a major driver of new activity.
“Many predicted that backlog would have dipped by now and that has yet to transpire,” said Basu. “What’s more, many contractors expect sales and staffing levels to climb over the next six months, while profit margins are projected to remain stable.”
But Basu warns that “backlog could dry up” fast.
“Anecdotal evidence suggests that banks are more cautious in their lending to the commercial real estate and multifamily segments,” says Basu. “Fears of recession this year remain pervasive in an environment characterized by high and rising interest rates.”
Coincidentally, architecture firms reported in November a second month of falling demand for design services, according to The American Institute of Architects’ Architecture Billings Index. The measure of architecture billings is considered an indicator that offers a glimpse into nonresidential construction spending nine to 12 months out.
The pace of decline during November accelerated from October, posting an ABI score of 46.6 from 47.7 (any score below 50 indicates a decline in firm billings). Inquiries into new projects slowed but remained positive with a score of 52.0, however new design contracts remained in negative territory with a score of 46.9.
“It’s a competitive world out there – and it seems more so than pre-pandemic,” says Kevin O’Shea, with Hydro Mobile. “There is way more product pick-up by major GCs than previously. More GCs are bringing in MCWPs under their auspices in a ‘total envelope management’ process where the GC will provide, and schedule, all the required façade access for its sub-contractors.”
CONNECT WITH THE TEAM

