New Powertrain Test facility at Cummins plant in Darlington, UK
18 July 2024
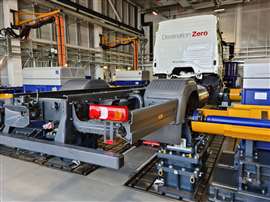
Cummins has opened a new Powertrain Test Facility at its engine manufacturing site in Darlington, UK.
According to Cummins, the new facility is the only one of its type in Europe.
The all-new installation, built at a cost of more than £13 million ($16.9 million), can accommodate a variety of vehicle types, carrying out a series of powertrain tests covering power delivery, emissions, fuel economy and longevity.
In addition to carrying out comprehensive testing of powertrains as fitted to vehicles, the facility is set up to evaluate engines using any of a range of fuel types, including diesel and biofuels. Further, the centre has been designed to accommodate testing of battery-electric drivetrains and hydrogen internal combustion engines.
With regards to hydrogen, the test area features a series of safety checks. These include sensors placed around the vehicle and the interior of the facility to monitor for fuel leaks. The interior walls are designed to protect test engineers in the event of an explosion, while exterior walls have specially-designed plates to help alleviate blast pressure.
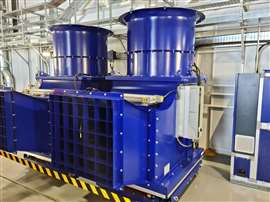
Additionally, the HVAC system is capable of renewing all air in the chamber more than once per minute, which helps to prevent build up of dangerous gas pockets.
The Powertrain Test Facility is intended to support Cummins as it looks to extend its capability as a full drivetrain designer and manufacturer. The new installation will support development of new powertrains which are more efficient, improving overall sustainability in operation.
Central to the new facility are a series of dynamometers. Unlike a rolling road, these are attached directly to the vehicle axles, as this allows collection of more accurate performance data.
The test facility can accommodate vehicles ranging in size from pickups and SUVs through to 44-ton trucks and double decker buses. While many of these only use one driven axle, both front and rear axles can be hooked up to dynamometers. With front and rear axles connected and driven, onboard systems assume that the vehicle is being operated on a road, rather than a test rig, again helping to deliver accurate data.
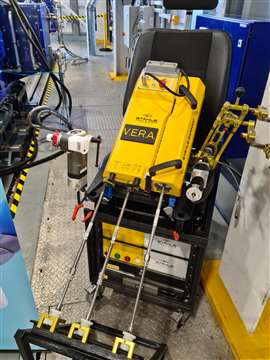
All drivers will operate a vehicle in slightly different ways, making it difficult to replicate test procedures and achieve standardised data collection. To get around this, powertrains under test will be driven by a robot driver.
This driving system is called the Virtual Engineer Robotic Assistant, or VERA. A competition to name the robot was held at a local primary school.
In addition to supporting development of more efficient powertrains, the new facility has other features which reduce its operational impact. In one case, the dynamometers will deliver electricity which will be used across the Darlington engine assembly site.
CONNECT WITH THE TEAM

