Highlights from Hillhead: What did you miss?
03 July 2024
The Hillhead 2024 event was held at the Hillhead Quarry in Buxton, UK from June 25th to 27th.
The event highlighted quarrying, construction, and recycling equipment and took place during some of the warmest days in the UK. Over 600 exhibitors presented new machines and services over three days with live demonstrations taking place at three specialist areas; quarry face, rock processing and recycling.
The organisers, the QMJ Group, reported that the show was the ‘most visited show ever’ in terms of the volume of visits over the three days, with visitors spending more time at the show than previous. In total, there were 26,626 visits over the three days which is estimated to be 8% higher than the last show in 2022.
Construction Briefing outlines just some of the highlights that were on display.
What did you miss?
SITECH
SITECH UK & Ireland, an authorised dealer of Trimble Civil Construction Field Systems, unveiled Trimble’s latest advancements in machine control and guidance technology.
The new offerings on show include the new 10-inch Trimble TD540 Display – offering increased memory and processing power over the TD520 – as well as an intuitive user experience with the Trimble Earthworks Grade Control Platform.
Accompanying the TD540 was the new MS976 GNSS Smart Antenna, which is a fully integrated GNSS positioning receiver plus antenna intended for rugged chassis or on-machine cab mounting implementing the latest Trimble Maxwell 7 Custom GPS chip and ProPoint Real-Time Kinematic (RTK) engine. This allows for more signal tracking and faster system initialisation times when satellite lock is lost and improved operation near obstructions is needed.
Also on display was the new entry-level Trimble BX992 Receiver, which incorporates the ProPoint RTK engine, and broadens the market with an additional dual GNSS receiver option combining with two Trimble Zephyr 3 Rugged antennas with all constellations included.
“What’s truly groundbreaking about our new positioning technology is its ability to maintain accuracy and continuity in situations where our competitor’s systems struggle,” said Brian Core, UK Regional Sales Manager at SITECH.
“In the past, if you lost clear sight of the sky due to trees or surrounding buildings, you’d have to stop and switch to a different method of working, which could potentially lead you to revert to the old way of working with profile boards and batter rails which consumes both time and costs. These latest solutions enable operators to keep working, even in tricky environments like dense forests, and hard up against buildings that were previously off limits for machine control.”
JCB
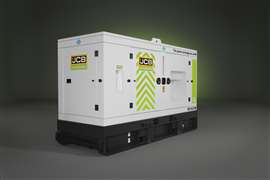
As part of its Waste & Controls option package, JCB has introduced the Intelliweigh system for its 427, 437 and 457 wheeled loader models, providing an accurate, digital and connected on-board weighing solution straight from the factory.
JCB Intelliweigh, which comes with an optional printer, has been specifically designed and developed for JCB wheeled loading shovels.
It is capable of weighing loads on a multitude of attachments even when working on uneven ground conditions, leading to reduced cycle times and maximum tonnes per hour performance.
Offering a +/-2% accuracy rating and an ergonomic 7” touchscreen display with physical keys for increased useability, the Intelliweigh system is compatible with up to 10 different attachments, including forks and buckets.
In addition, the company unveiled a generator powered by a JCB hydrogen combustion engine at the show. The G60RS H genset offered a glimpse into the future of zero-carbon worksites and highlights how the JCB hydrogen generator delivers the same power, performance, and efficiency as its diesel equivalent – but without the carbon.
JCB showcased how a hydrogen generator works in tandem with JCB’s three-phase Powerpack to create on-site ‘microgrids’ – utilising both battery-electric and hydrogen combustion technology. With energy supplied to the Powerpack from renewable sources, the generator, powered by hydrogen, effectively becomes a battery charger, only running for short periods when the battery needs topping up, or at peak load points. This reduces fuel consumption and offers long periods of silent or quiet hours of operation.
CDE
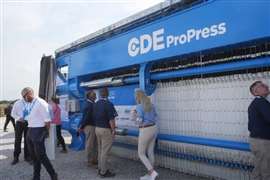
CDE unveiled its new ProPress high-performance filter press at Hillhead, adding to its water management and recycling systems.
Developed to meet the evolving needs of the construction and demolition (C&D) waste recycling, quarrying, and mining sectors, the ProPress is said to integrate the latest technological advancements to deliver operational efficiency and maximum water recovery.
The company says that the ProPress, which features patent-pending technology, benefits from a flexible design and variable throughput that can be scaled to fit the processing volume of any operation.
The ProPress system differs from traditional filter presses in that it is dual feed, allowing sludge to be fed from both sides. This results in improved efficiency and faster cycle times says CDE.
The system also features optimized sludge feed pressure for faster dewatering and increased throughput. Additionally, its overhead beam design reduces stress on the unit, enhancing reliability and durability.
The ProPress comes with larger plates (2.5m x 2m), providing greater chamber volume and requiring fewer plates.
CDE adds that the integrated plate-shaking technology helps prevent filter cake build-up within chambers, reducing the need for manual intervention. The system also includes an access walkway for safe and unobstructed maintenance, as well as flush-mounted drip trays that secure the maintenance platform and reduce material entrapment.
A robot serves as the main workhorse for the ProPress, controlling plate opening, plate shaking, cloth washing, plate winch, and the maintenance platform.
The CDE ProPress is offered in various sizes to accommodate different markets and applications. Additionally, it comes largely pre-assembled to expedite commissioning.
HD Hyundai Construction Equipment
HD Hyundai Construction Equipment introduced two heavy crawler excavator models and its largest wheel loader, at the Hillhead 2024 quarry exhibition.
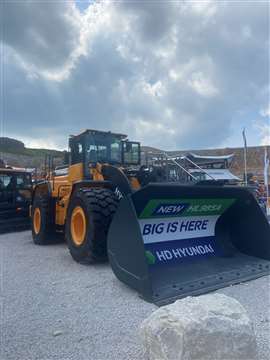
The company announced its largest Stage V crawler excavators, with the arrival of the 80-tonne HX800A L and the 100-tonne HX1000A L.
The heavy-duty machines are said to have been designed to operate in mines and quarries, as well as in bulk earthmoving for construction and infrastructure project applications.
Both excavators are powered by Perkins diesel engines with the HX800A L using the six-cylinder Perkins 2506J, providing 400kW (539hp) at 1,800rpm and 2,468Nm of torque at 1,400rpm. The larger HX1000A L is powered by the Perkins 2806J, offering 460kW (629hp) at 2,000rpm and 2,952Nm at 1,300rpm.
Hyundai says that an electronic hydraulic power control system minimises fuel consumption while increasing digging efficiency. It utilises nine sensors across the machine to calculate the required flow and pump output.
The HX800A L has two variable displacement tandem axial piston pumps, each delivering 504 lpm of flow, while the larger HX1000A L has three pumps producing 523 lpm each. A closed-centre main control valve ensures that there is minimal hydraulic flow in the stand-by position, reducing fuel use.
In both machines, the pumps have a cross-sensing system to reduce fuel use and to ensure that dig-end hydraulics operate independently.
The HX800A L is suitable for 4.25-5.24m3 buckets and the larger 100-tonne machine will be able to work with 5.4-6.8m3 buckets.
The two machines are offered with a choice of short mass excavation and longer monobooms, and with the option of two dipper am lengths. To ease assembly on site, the counterweight is mounted horizontally and a hydraulically-removable counterweight is available as an option.
Terex
Terex Materials Processing (MP) demonstrated sustainable innovation at Hillhead 2024 with a display of 19 products across six of their brands.
“Hillhead has always been a major event in the Terex MP trade show calendar and our presence this year underscores our position as a powerhouse in the aggregates industry,” said Pat Brian, vice president, Terex Aggregates.
“Our impressive line-up, of which eight are new products, reinforces our strong portfolio of customer-focused products that are paving the way for a sustainable future.”
In the demo area, Terex MP featured the new Powerscreen 1300X Maxtrak cone crusher, EvoQuip Bison 220R jaw crusher, Finlay electric I-120RS impact crusher, Finlay electric 883+ scalping screen—both of which were powered by the new Finlay TG500 tracked generator.
On the stands, Terex launched new products including the Terex Washing Systems STREAM software, Terex MPS WG220E portable cone crusher, and the Finlay C1550+ hybrid prototype. Other existing products featured on the stands included the Powerscreen Titan 600, Powerscreen Warrior 1400XE (hybrid), Finlay J-1170+, EvoQuip Caiman shredder, MDS M412 recycling trommel and a range of equipment from Terex Washing Systems’ feeder to filterpress solutions.
Terex says that they recognise that there is no one-size-fits-all solution and that electrification is just one part of Terex MP’s alternative power strategy, which aims to develop flexible options that adapt to the user’s preferred energy source.
An £8.1 million (€9.5 million) project with CATAGEN—a catalyst testing expert developing new technologies in green hydrogen and efuels—will deliver a decarbonised end-to-end demonstration of a Powerscreen Premiertrak 450E crusher and Chieftain 1700XE screener, powered by green hydrogen and e-diesel at a working quarry site in Northern Ireland in 2024.
CONNECT WITH THE TEAM

