How one contractor is processing a million tonnes of excavated material
03 July 2024
Safir Proje, a specialist earthmoving, demolition, road construction and tunnelling works contractor, has begun the mammoth task of processing over one million tonnes of excavated material from a construction site at the Istanbul Financial Center (IFC) financial services hub in Istanbul, Turkey.
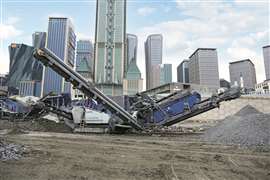
The contractor has deployed a Kleemann’s MOBIREX MR 130i EVO2 impact crusher and a MOBISCREEN MSS 802i EVO mobile coarse screening plant for the project, which will see the excavated material used for concrete production and road substructures in the heart of the financial district.
Feyzullah Kahraman, Managing Director of Safir Proje, said: “We will be working here in the centre of Istanbul for about one and a half years.
“We have to be especially flexible at this location, both in terms of the particular environment and the material.”
Depending on the weather, the 0-500/600 mm feed material is at times wet and muddy, at other times dusty and dry. In order to ensure it had the required flexibility to carry out the project, Safir Proje chose to purchase the Kleemann plants specifically for this application.
In wet weather, the MOBIREX MR 130i EVO2 impact crusher is preceded by the MOBISCREEN MSS 802i EVO coarse screening plant.
This combination loosens the sludgy material, screens it coarsely and prepares it for feeding to the impact crusher. The first step is not required in dry conditions and the excavated material can then go directly to the impact crusher.
“It has been shown that this combination produces the very best results,” says Feyzullah.
“We produce grain sizes of 0/38 and 0/63 and, depending on the end product, can achieve an hourly output of 200 to 300 tonnes with a consumption of 24 litres.”
He added: “The impact crusher meets the requirements for the cubic material very well. I’ve never achieved this quality before.”
According to Kleemann, the fact that only one machine needs to be refuelled in dry conditions when the impact crusher is running without pre-screening is very cost-effective.
The OEM said: “It results in a noticeable reduction in operating costs. And the coarse screening plant can then easily be used for other projects.
“With its proportionally controlled travelling gear, it can be moved quickly and easily. Set-up times are short, partly because the side discharge conveyors are folded instead of dismantled.”
Feyzullah and Kleemann worked closely to achieve the required set-up for the IFC project and today, operations at the Istanbul site are running smoothly.
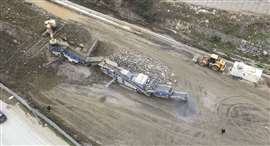
CONNECT WITH THE TEAM

